製造業が抱える5つの難問は以下となります。
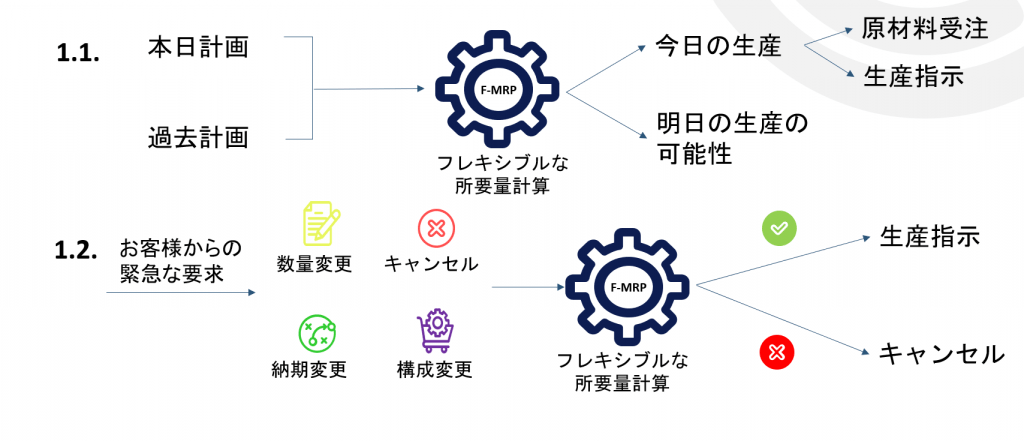
TPiCS-Xはオーダーリリースした計画でも状況に応じ修正することができます。また、TPiCS-Xはオーダーリリースした計画も包含して所要量計算します。
オーダーリリースした計画をベースに今回の生産(受注)が成り立つか否か、シミュレーションをしながら所要量計算をします。
TPiCS-Xは現在在庫を起点に、本日も過去も、全ての未完の計画を前提にして所要量計算しますので、今日の受注に対応した今日の生産、明日の生産が可能か否かが分かります。TPiCS-Xではシミュレーションしながら生産計画を作り、部品や材料の手配をしていきます。
それに対し一般的なMRPシステムは、在庫の引当てやロット纏めをして必要数を計算し、伝票を発行したら、後はシステムとしては面倒を見ないので、間近な計画変更や、明日の生産に必要な部品が本当に足りているかなどは、電卓を叩いて計算する必要がありました。
TPiCS-Xの場合は生産計画の全てをシステムに任せることができます。しかし、システムに任せる(計算させる)為には、計算させるデータが意味のあるものでなくてはなりません。システムが持っている在庫数やマスターは勿論、システムが持っているオーダーリリースした計画データも正しくメンテナンスされている必要があります。これを我々は「計画管理」と呼び、計画管理をしながら短納期生産を実現していきます。
このほか短納期生産を実現するためには「平準化の問題」や「現場指示の問題」「サプライヤーの問題」などもあります。それらについて小冊子〖製造業が抱える5つの難問をTPiCSで解く〗をご覧ください。
「見える化」には二つの面があります。
①5Sに代表される現場改善による見える化
②システムの画面を見て分かるようにする見える化
システムによる見える化は、上記の「計画管理」を行っていけば自ずと実現できるようになっていきます。
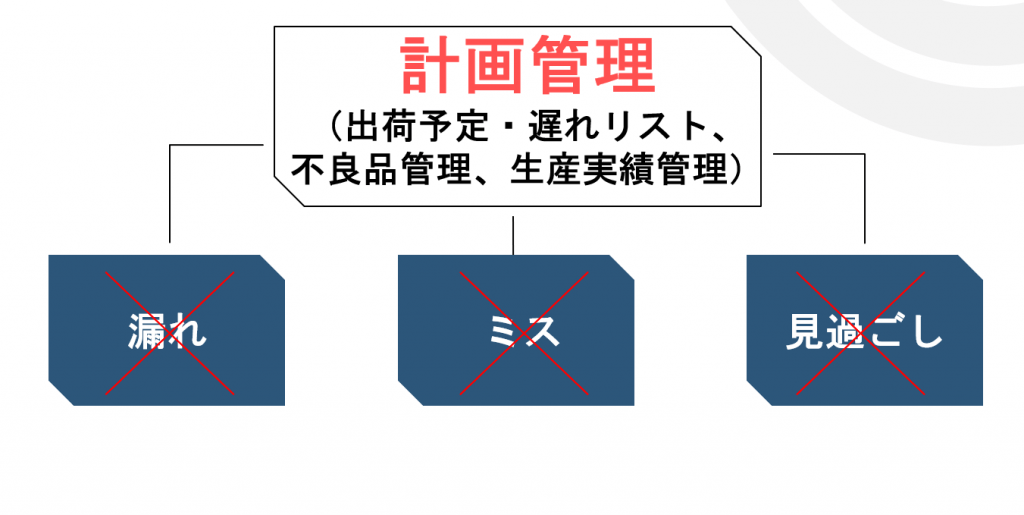
地震や落雷などの災害や大事故による出荷遅れはTPiCS-Xを使っても防ぐことは出来ませんが、普段の仕事の中での「ミス」や「漏れ」、「見過ごし」等による生産トラブルは上記「計画管理」を行いトラブルを予見できる仕組み作りを行えば、減らしていくことができます。
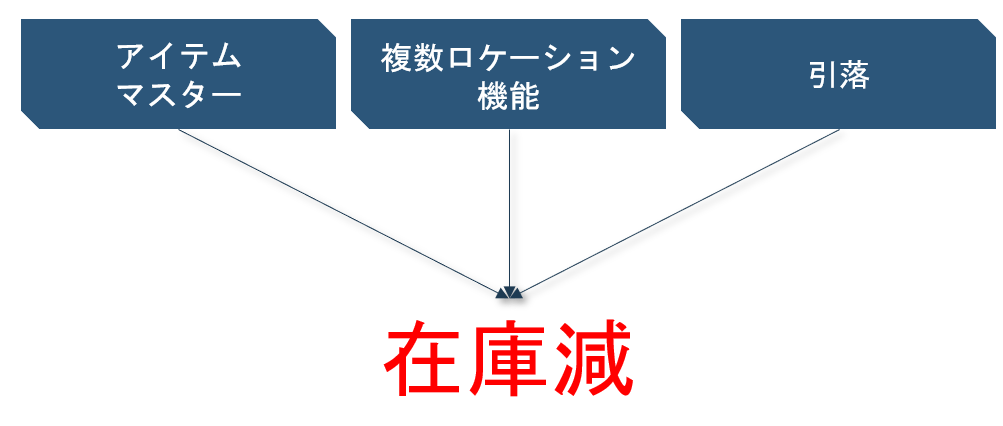
在庫を発生原因により二つに分類して考えます。
①ミスや見込み違い、設計変更などによる不良在庫
②日々の生産活動の中で発生する運用在庫
不良在庫の原因を更に分析すると、複数の要素が複雑に重なり合って発生していることが多く、簡単な対応策などは見つかりません。この問題に関しても答えは「地道な改善」になります。
TPiCS-Xには設計情報を正確に、速く、簡単に、しかも設計変更まで含め、生産情報に反映する仕組みがあります。これによりこの問題の半分は解決できます。
見込み精度はTPiCS-Xの範囲外なので、見込み違いがあっても被害を最小限に止めることを考えます。その為にはロットサイズを小さくし、発注リード日数を短くします。しかしこの方法はそれぞれまた別の問題がありますが、それらについては小冊子の〖製造業が抱える5つの難問をTPiCSで解く〗をご覧ください。
運用在庫も二つに分けて考えます。
②-1手配担当者が変化に対応する事を考え、「勘と経験」で発注数を調整していて、それに起因する在庫
②-2工場に入ってから出るまでの必然的に生じる在庫
発注調整による在庫は、TPiCS-Xには「変化に対応するためのバッファ」が設定できるので、「勘と経験」に頼る仕事ではなくシステムで管理された仕事に変えることにより在庫を減らします。
入りから出までの在庫は、「納入リード日数・製造リード日数」と「ロットサイズ」で制御できます。
「計画管理」が実現出来ている状態だと、これらの設定を小さくしていくと計画通りに生産できなくなる臨界点が分かります。するとそこが在庫縮小の為のネックですからそれを改善していきます。
生産管理の難しさや大変さの本質は「変化・変更」にあります。そしてその源は「見込みが実需になる時の数と時期の変化」と「設計変更」です。
TPiCS-Xには「構成情報変換オプション(「在庫を減らす」で触れたもの)」があり、設計変更を生産情報に反映する機能の他、既に手配されているものとダイレクトに照合し、キャンセル伝票を発行したり、追加の伝票を発行することも出来ます。