- Achieving the production for short-term delivery and ready for whatever changes come along
- Attempting to make the factory floor observable
- Solving the problem of delay
- Balancing inventory reduction
- Handling short-term turnaround of new products, and engineering changes
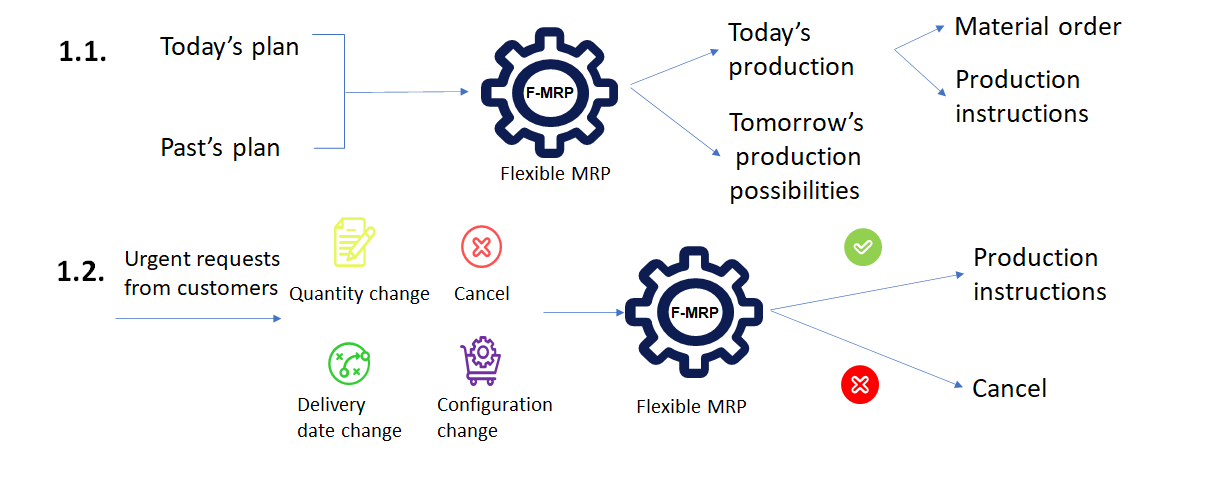
TPiCS-X can be modified according to the situation even in the order release plan. In addition, TPiCS-X also includes the order release plan and calculates the material requirements.
Whether or not this production (order) will be realized based on the the order-released plan, TPiCS-X will calculate the material requirements planning while doing simulation.
Because TPiCS-X calculates MRP based on the current inventory as a starting point, as well as all incomplete plans for today and in the past, users can see whether today’s production corresponding to today’s order and tomorrow’s production are possible. TPiCS-X creates a production plan and arranges parts and materials while simulating.
On the other hand, the general MRP system calculates the material requirements by allocating inventory and lot sizing. After issuing the slip, because the system will not take care of it so it was necessary to hit the calculator and calculate whether the parts needed for tomorrow’s production were really enough.
With TPiCS-X, all production planning can be entrusted to the system. However, in order to entrust (calculate) to the system, the data to be calculated must be meaningful. In addition to the number of stocks and master data held by the system, it is also necessary to maintain the order release plan data held by the system correctly. We call this “plan management”, and we will realize short-term production while managing the plan.
In addition, there are “leveling problems,” “on-site instructions problems,” and “suppliers problems” in order to realize short-term production. Please see the booklet 〖Solve the five difficult problems the manufacturing business faces with TPiCS〗 about them.
“Observation” has two aspects.
①Observation through on-site improvement represented by 5S
②Make it clear by looking at the screen of the system
Observation by the system will naturally become possible if the above “planning management” is carried out.
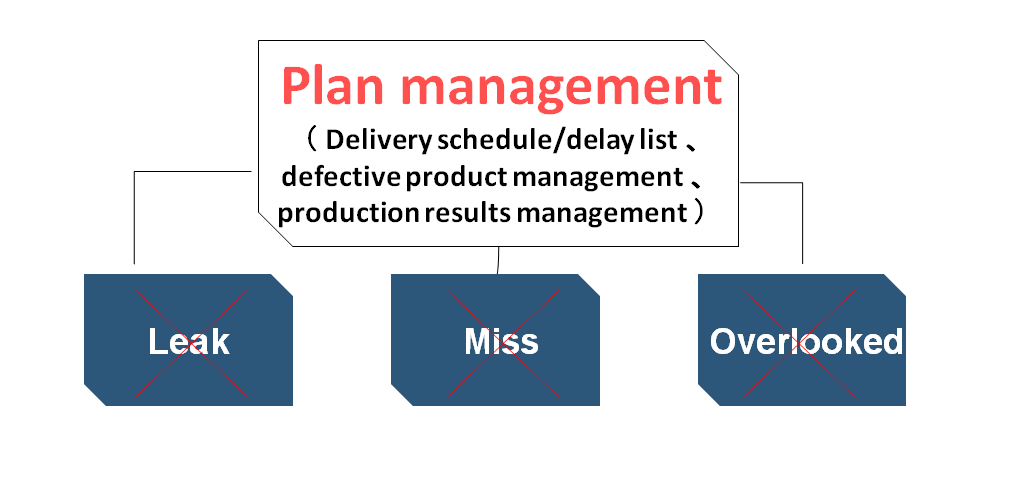
Although TPiCS-X cannot prevent delivery delays due to disasters such as earthquakes and lightning strikes, and major accidents, Production troubles caused by “Miss”, “Leak”, “Overlooked”, etc. in everyday work can be handled by the above “planning management” and creating a system that can foresee troubles.
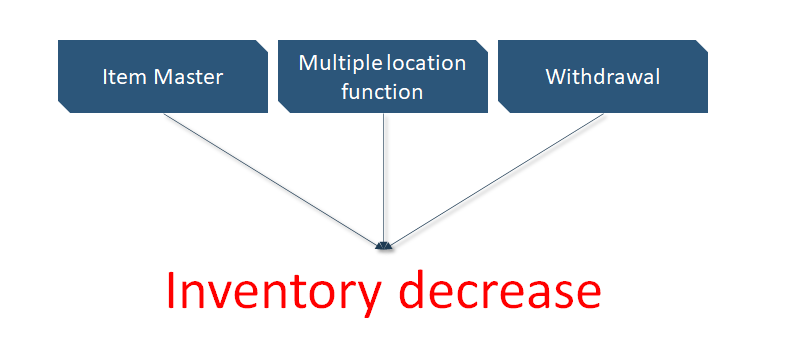