- Management needs of the manufacturing industry
After conducting surveys with our customers, we found that manufacturing enterprise have the following management needs:
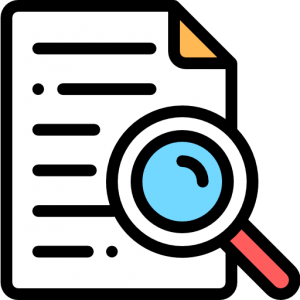
- TRACEABILITY
On September 10, 2016, Samsung Electronics Co Ltd – Korea’s leading electronics manufacturer – called the owners of Galaxy Note 7 phones to stop using and exchange them, after having reports of fires or explosions in the phone’s battery while charging.
Notification recall of Galaxy Note 7 phones global related at least 10 countries
Plan to recall 2,5 million Note 7 phones are launched after 2 weeks of the official sale, something that never happened to Samsung. After the recall, Samsung had to perform a series of investigations of large scale to find out what is the cause of fires or explosions batteries. The investigation requires Samsung have to find each delivery sheet, production directive sheet, QA sheet, report in each production process on all shipments. This takes a lot of time and costs billions of dollars for Samsung.
To avoid having the same problem, many manufacturing enterprises hope to be able to quickly trace root source off products to be immediately removed problematic production shipments, avoiding sending defective products to customers.
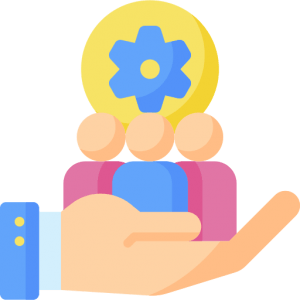
- MANAGEMENT BY 4M1E
Management according to 4M1E means specific management to each:
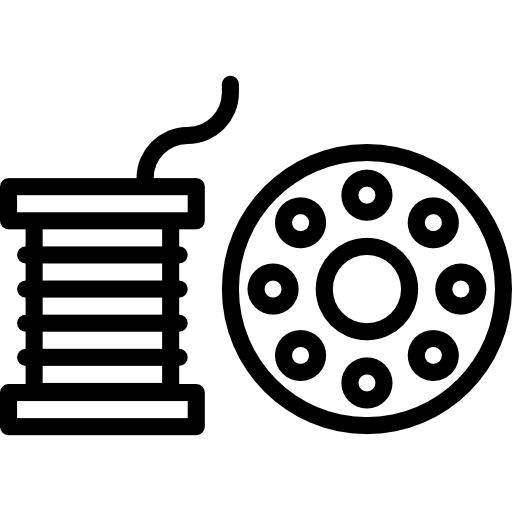
Material
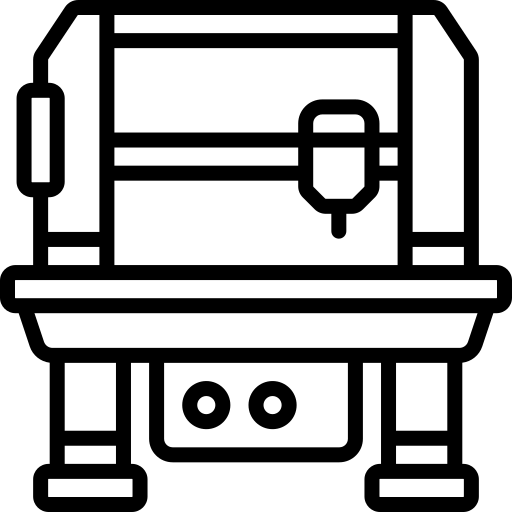
Machine
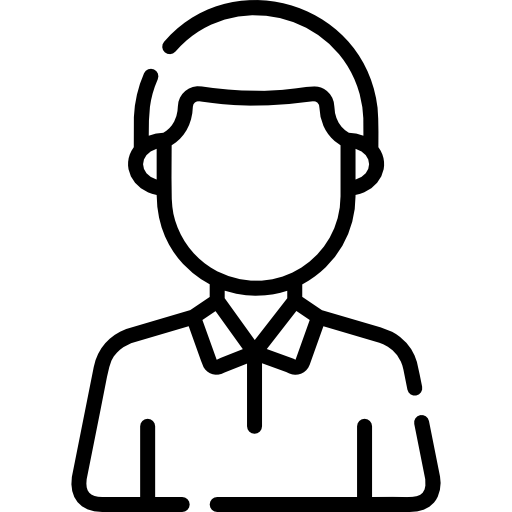
Man
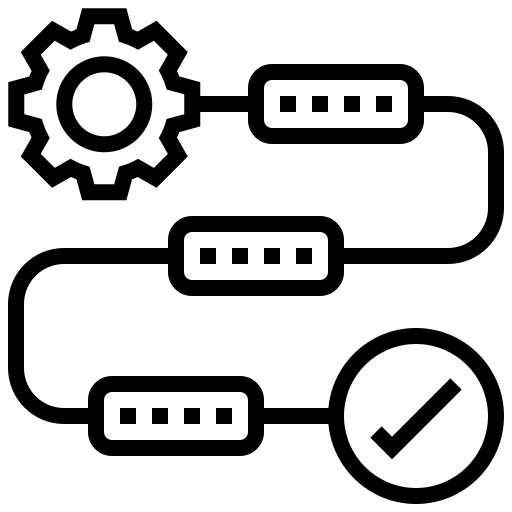
Method
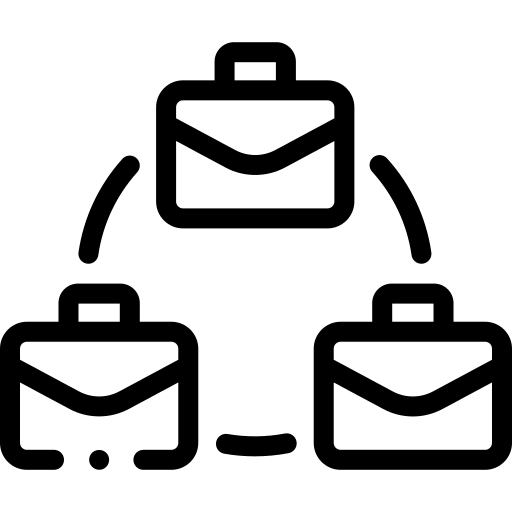
Environment
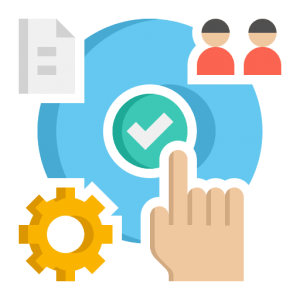
- QUALITY MANAGEMENT
Quality management is specific management according to each quality category of the material, finish products, non – finish products, machines, and processes. All of the checklists need to be archived and quickly accessed whenever people need them.
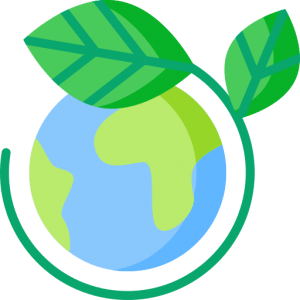
- ENVIRONMENT
Annual, manufacturing enterprises throw out tons of waste paper incurred from processes such as shipments, import, issue production directives sheets, quality check, certificate,… This causes a lot of harm environment of people and the costs to treat this type of waste are also very big. So manufacturing enterprises have green living trending and protect the environment.
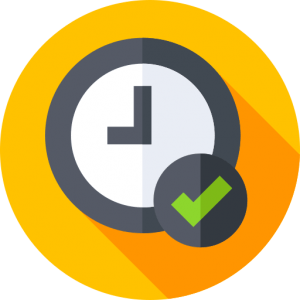
- FLEXIBLE, FAST AND REAL-TIME DATA
We are living in an area of digital transformation, where all the information, data need to be updated fast to be able to rate and edit the fastest, from that help, we sucess fast and avoid unnecessary risks. Such an analogy, manufacturing is an industry that requires information sources must be concentrated and to be updated fast, timely, real-time for managers to anticipate risks that can happen such as defective products, delay in delivery, or delivery error, from that make appropriate adjusted fit. So, flexible, fast, and real-time data are keywords that are very interested in today’s businesses.
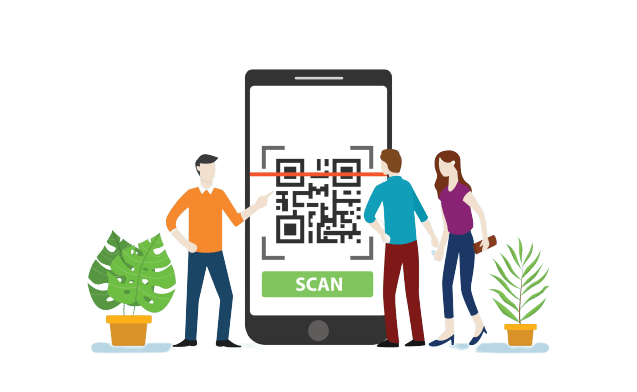
- DXFACT – Production management system by QRcode
Production management system by QRcode replaces all of the kinds of papers used in processes such as import warehouse, warehouse transfer, ex-warehouse to manufacturing, production directive, ex-warehouse, stage check, product QA,… by QRcode, RFID card, handheld QR code scanner, phone. With the use of this system, the staff takes less manual work, saves unnecessary time, increases labor productivity, and minimizes errors caused by data entry. Special, all of the data scanned by QRcode scanner is real-time data, imported into the system right after scan (in fact only slow 0.01s). All of the data stored on the server, users with only one click will be able to immediately find specific information about products or materials without spending too much time checking documents or searching for information in Excel. The application of this system will help save time spent on document synthesis, data entry, printing costs, labor, minimize the errors caused by the data entry process.
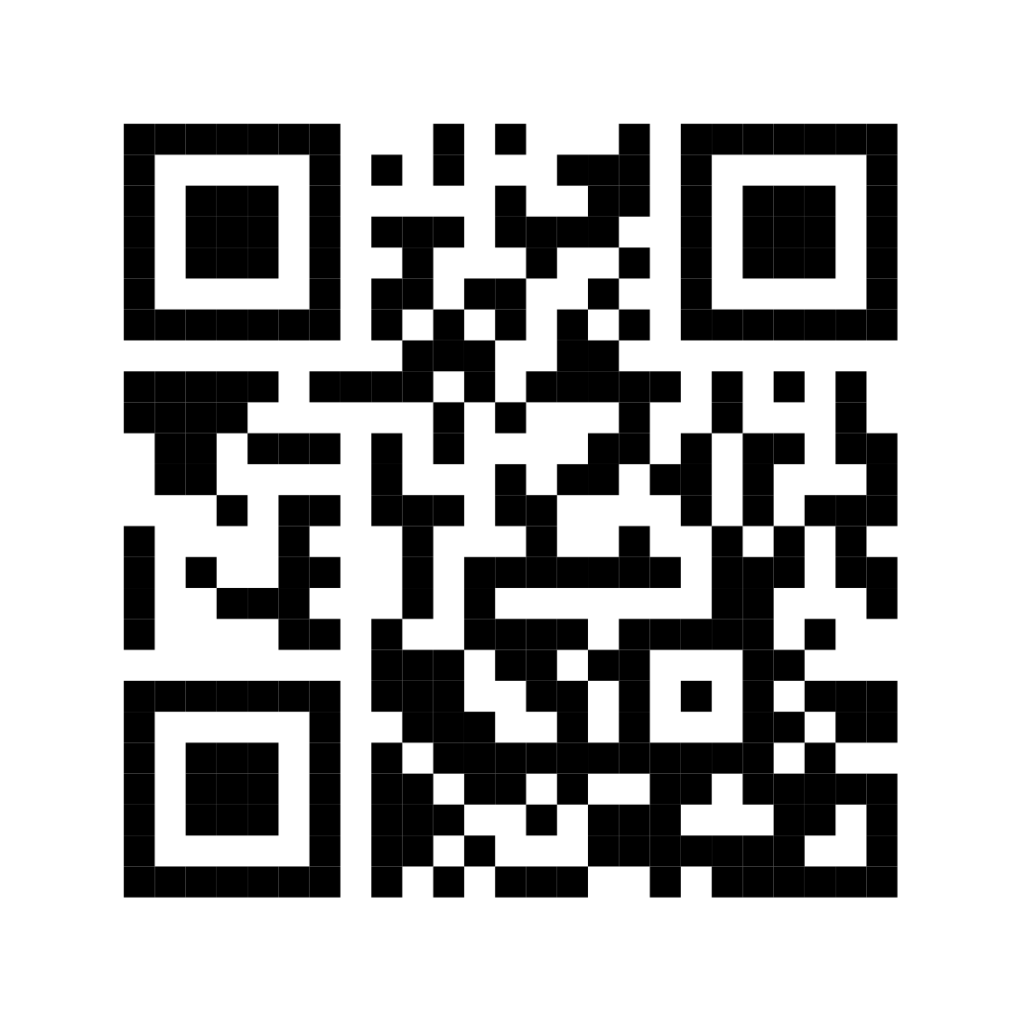
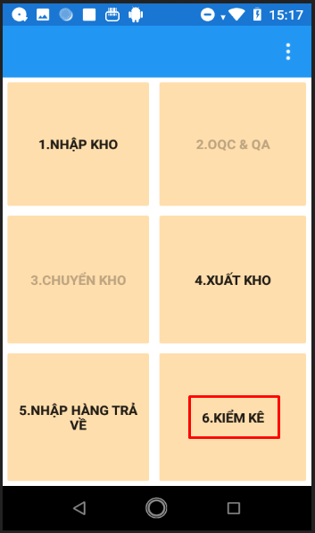
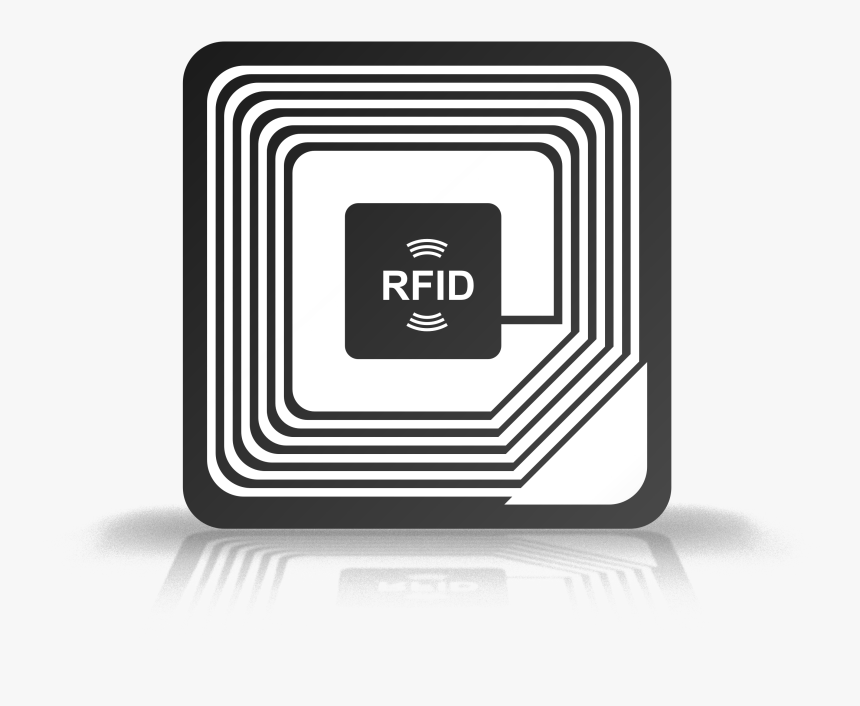
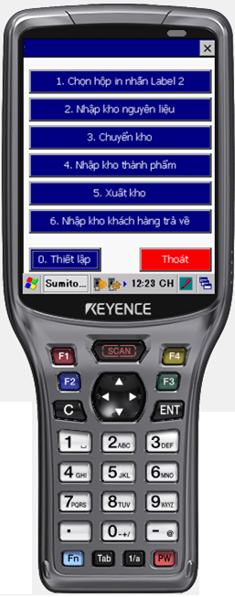
DXFACT Includes 5 main modules:
- Inventory management
Materials and finished products before the import warehouse will be labeled with a QR code. Users will use a dedicated scanner to scan that QR code before importing warehouse, transfer production warehouse, or ex-warehouse. When scanning the code, the machine automatically counts the quantity and confirms the quantity of the actual import warehouse. Each QRcode will contain information including:
- With materials is code, material name, supplier name, Lot No., actual input quantity, location,…
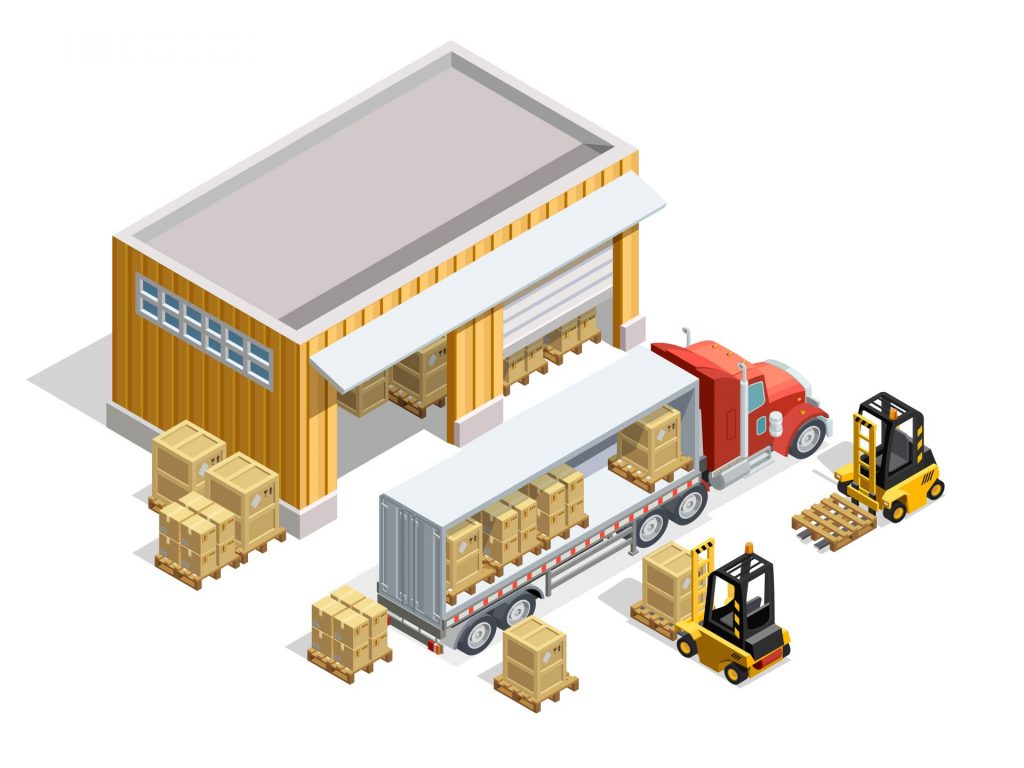
- With finished products (semi-finished products) as code, finished products name (semi-finished products name), Lot No., stages, quality test results, the actual quantity, location
The information on the QRcode will be set up depending on the user’s management needs. After scanning, all information will be sent directly to the server without the need synthetic for paperwork or data entry. This module includes the following functions:
- Lable management
- Input warehouse
- Ex-warehouse
- Control Lot No
- Manage by First In First Out
- Control shipping
- Shipping
- Inventory (By mobile)
- Link to other systems
- Process control
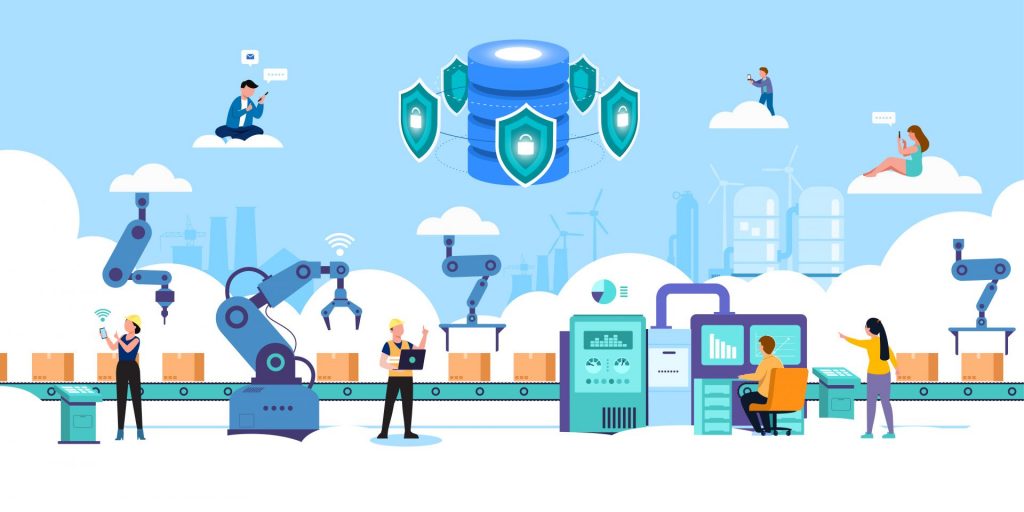
This module helps users manage actual production stages through the Keyence scanner and PC. A QRcode containing information corresponding to the user’s management needs will provide each stage, materials, machines, labor. A QR code can contain information such as:
- With the materials as code, material name, supplier name, Lot No, the actual quantity of input transferred to the stage
- With the stage as a production directive, stage code, stage name, machine code, machine name, production information, test results, completion status, etc
- With labor as the code, full name, office, department, etc
Users can check all information obtained during production has been saved in production history when needed. Users can also export data to a CSV file. This module includes the following functions:
- Check the production status of each stage in real-time
- production history control
- 4M ( Man, Machine, Methol, Material)
- Quality Control
- Link to other systems
- Quality management
We move quality control tasks from paper to mobile devices (Android OS) and tablets. Users can scan QRcode with these devices and make the items they want to check. All test results will be saved on the server for use when needed.
Besides, In order to ensure stable operation and avoid unnecessary risks affecting production progress, daily/periodic inspection of machines is an indispensable job. But in reality, there are cases where the worker only ticks the inspection papers to confirm without ever going down to check directly. To prevent this problem of fraud, we will assign machines and devices an encrypted QR code.
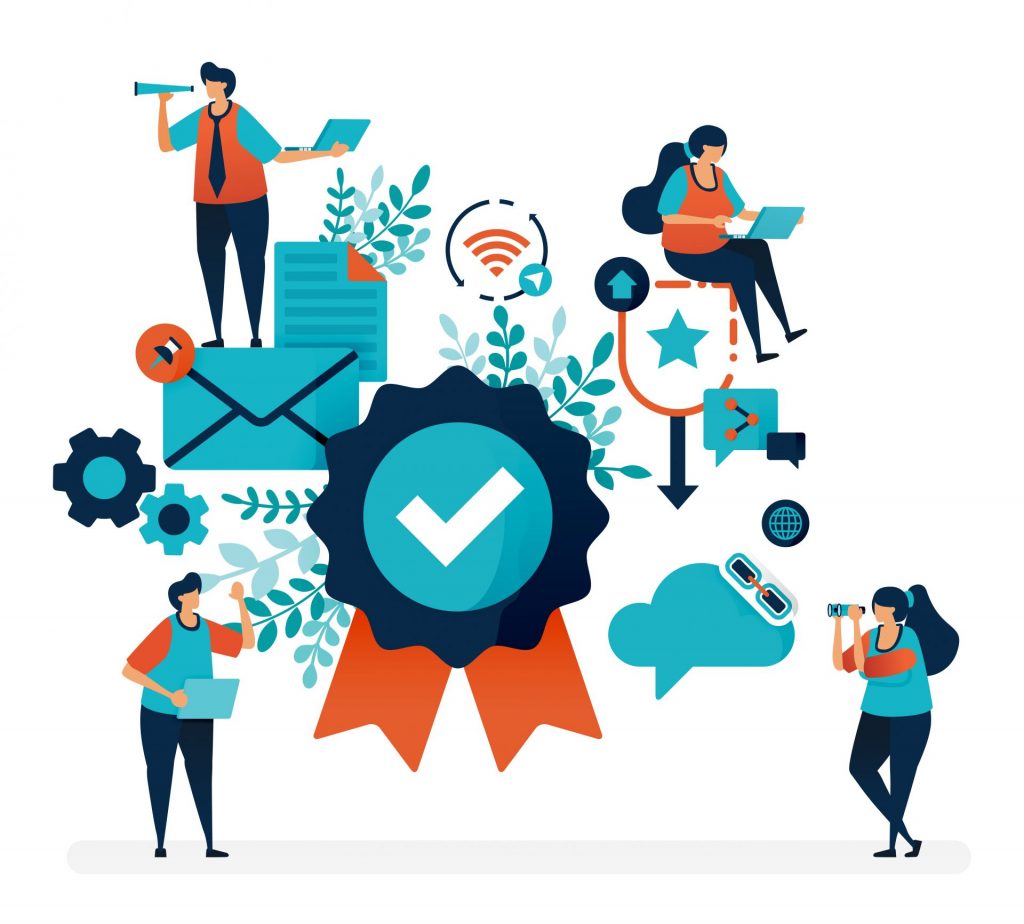
The labor is obligated to come down to the place, scan this QRcode with a mobile device (Android OS) or tablet to conduct the inspection. These mobile or tablet devices have fixed time settings for each test item. So users won’t be able to accumulate indiscriminately to finish quickly. After that time, it is allowed to move on to the next inspection item.
- Progress management
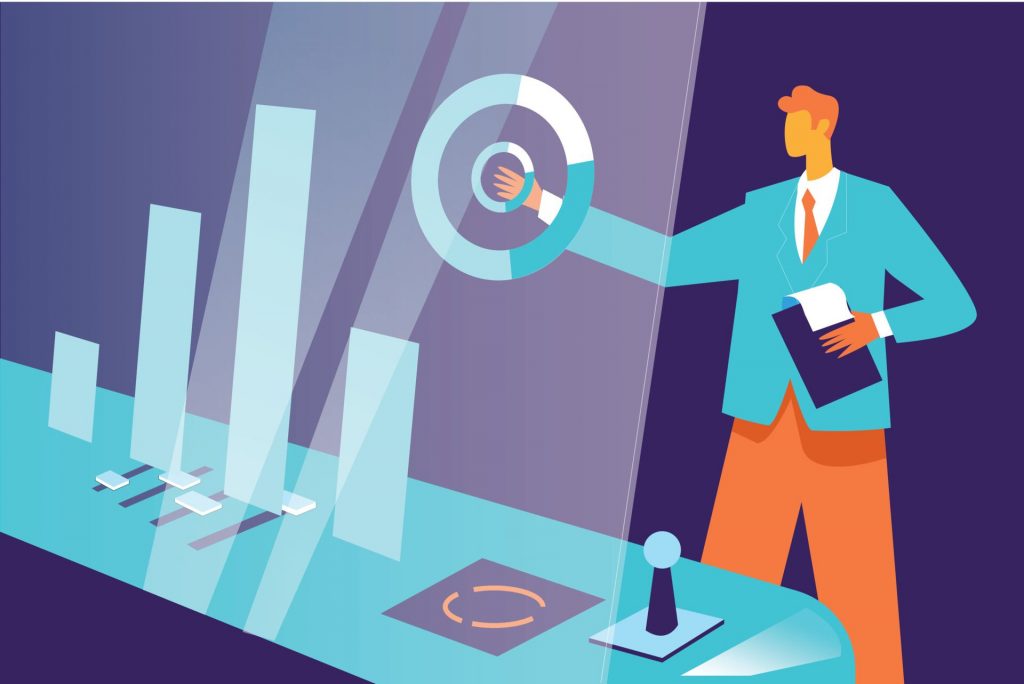
This module includes the following functions:năng:
- Actual production management
- Production supervision
- Warning production
- Production adjustment
- Connect IoT devices
The machines and the counter will be connected to the PLC to extract data. After that, the data obtained will connect to the productivity electronic board, then aggregate the data into the master server. The system will synthesize, analyze the data and provide information on the completion progress of orders in charts form. The system can give alerts to orders that are behind schedule so that the manager can push the production of that order.
- Traceability
Based on data collected from modules such as inventory management, stage management, quality management, schedule management, we have launched the module as traceability.
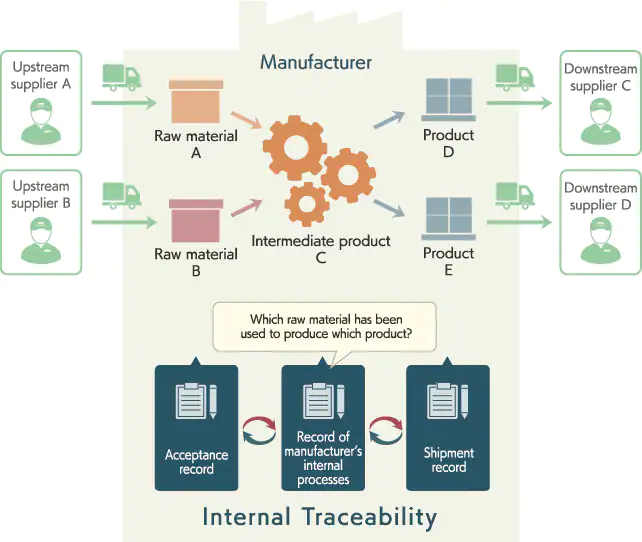
With just one click, users will know the finished products they are looking for:
- Belong which Lot, belong which location
- What materials are used, which supplier.
- How are the test results
- Which stage have you gone through, which machine, who is the producer
- How has the machine used to produce the finished product been maintained
- What export directive
- Has the goods shipped or not and delivered to any customers
Users can access forward and backward all relevant information without having to rummage through documents or search in excel anymore. As a result, when detecting defective products, users can remove all error products from the same lot, avoiding the production of error products to customers.
III. System benefits
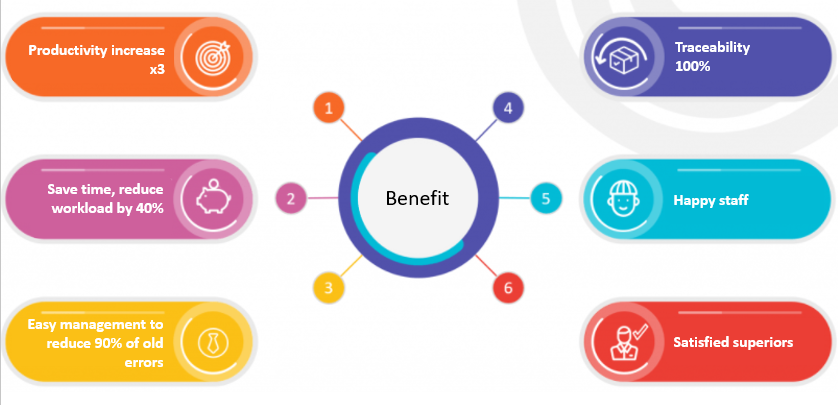