TPiCS has a total of 19 different options. You can to select the option that suits your factory management desires.
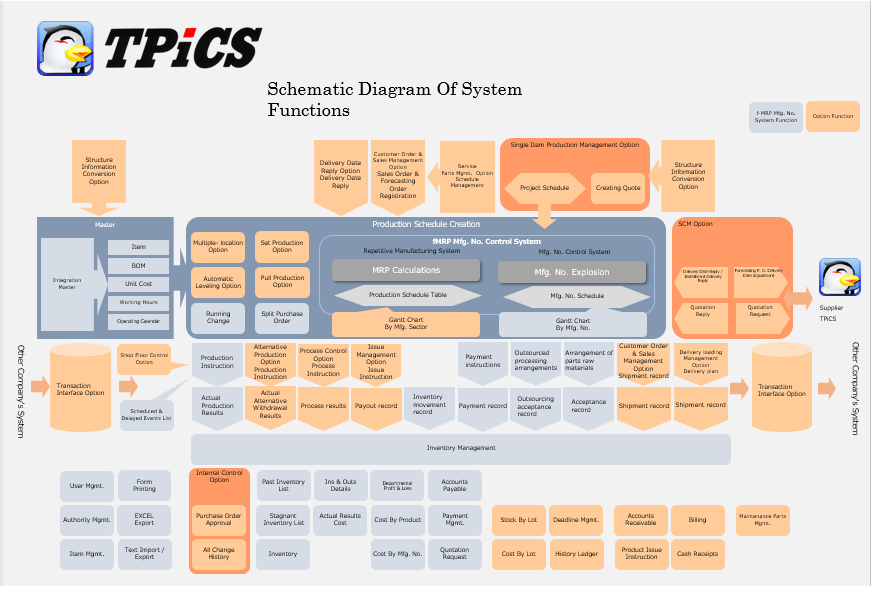
FROM THE SALES AND FORECASTING ORDER DATA TO THE PRODUCTION SCHEDULE
・ You can create the shipping schedule of TPiCS from the Sales Order data and perform the MRP calculations right away.
・ You can make arrangements for parts and materials based on the forecasting schedule by working together with the f-MRP function. Even if the forecasting schedule changes, you can advance to the next MRP calculations without doing anything since it’s based on the f-MRP function.
・ In receiving an order for the product that requires the mfg. no. control, you can create a Mfg. No. Schedule or allocate a sales order to the preceding Mfg. No. Schedule upon entry of the sales order. If the scheduled quantity to be allocated is insufficient, you can automatically create a Mfg. No. Schedule with as much as the insufficient quantity.
・ It’s possible to import the order and delivery instruction data that come from the Internet.
・ The file to be imported is in CSV format.
・ You can import sales orders from the system like EDI and ERP via the Transaction Interface Option.
・ It completely supports the daily delivery instructions.
・ You can reconcile and delete the forecasting data against the firm Sales Order data you are reading in.
・ It’s possible not to reflect them in the production schedule as backorders.
・ It’s possible to respond to the customer-order-receiving style of the Full Choice Option Production.
・ You can enter whatever level of the product structure for the Sales Order data. By this function, you could manage the OEM shipments and the repair parts at the stage of the intermediate products and the parts. The MRP calculations would take into account those required quantities.
FORECASTING DATA
・ In the case that the firm delivery instruction data are coming on a daily basis like the automobile industry, you can read them in while you had the forecasting data reconciled and deleted in the order of their delivery date for the same item and delivery location.
・ The processing of forecasting orders is available, separately from that of firm orders.
・ You can delete the forecasting data periodically and read in new data again.
Shipping Instructions
・ You can issue the shipping instructions up to the set number of days ahead from today based on the scheduled shipping date of the Sales Order data.
・ You can issue the shipping slip by narrowing down to only the products of which stock was available at the time of issuing the shipping instructions.
Actual Shipping Results
・ A warning message is displayed if the current inventory of the product falls below 0 at the time of entering the actual shipping results.
・ For shipping schedule, you can enter the actual shipping results and the actual results of acceptance completion after an arrival at customer’s site with the separate statuses. In the Inventory List, product inventory is withdrawn and you can confirm it as the quantity of non-acceptance at customer’s site. You can reflect an event in the Accounts Receivable Detail at the time of shipment, or at the time of acceptance at customer’s site.
・ When combined with the Traceability option, it’s possible to associate up to the intermediate process and the actual shipping results with the lot numbers of raw materials that were used, and to retrieve the used lot from the actual shipping results and the ship-to from the lot number.
Slip Form
・ The shipping slip, the packing slip, the invoice and the accounts receivable ledger are available.
・ The order list, and the scheduled shipments and the delayed shipments with a date specified are available.
Selling Price Registration
・ The system operation where the selling price varies depending on the ordered quantity or period is supported.
Billing, Cash Receipt Management
・ The cash receipt management where you reconcile individual invoices is possible.
・ Registering and displaying the overseas customer information in the native language is possible.
・ You can export the accounts receivable details for some accounting systems.
You can display the Gantt Chart that has been aggregated for each department based on the production schedule made by the MRP calculations and the mfg. no.
In the Gantt chart, the schedule that is over the production capacity of the department is displayed in red, so you can grasp the plan with high load. You can move the plan to other departments by drag & drop, adjust the plan back and forth, divide the plan and adjust the quantity. In addition, you can adjust the intermediate processes and materials in parent-child relationship with products in conjunction by drag and drop.
In the most recent plan, it is possible to aggregate from the Schedule Detail in which detailed production location was set, and when you register the machine in the production location, you can assign the work to the machine and adjust the schedule.
In the Multiple Locations Option, you can make a production schedule for multiple mfg. locations to one item according to their own parameters of the mfg. lead-time, the purchasing lead-time and the lot size.
With this function, you can make a schedule that will meet more complex situations. For example, you could make a production schedule to entrust to outsourcing depending on the workload of the mfg. department although you normally produce internally, make a production schedule to distribute the production volume to 2 places in the mfg. department according to the ratio, and make separate schedules for supplies for multiple outsourcing companies.
Also, you can simulate and adjust the bottleneck process from the journal that’s been displayed because of the sales order with a short-term delivery date by changing it with a drag-and-drop in combination with the Gantt Chart By Mfg. Sector.
You can manage the instructions and the actual results by exploding to the detailed process based on the Schedule Detail that was created from the production schedule made by the MRP calculations and the mfg. no. explosion.
By changing the routing code, you can re-do the explosion of the detailed process, as required, that was exploded according to the master tables at the time of creating the Schedule Detail. For example, you could register the routing when you used the old machine beforehand, changing the routing code of the original process when the load is high, and print the process order form where a setup is added to the regular order of operations.
The process is both possible for an operation for the use of only instructing work to the factory floor and for an operation where the actual results entry is required for working time and progress management of actual results. You can confirm and adjust the load by using the Gantt Chart By Mfg. Sector together.
You can instruct issues (picking) from the warehouse to the factory floor.
The issues will be summarized by item, issue-from and issue-to. (For the mfg. no. controlled items, they will be summarized by mfg. no. in addition to the above.)
You can register the lot sizes for arrangements and issues separately.
If the current inventory doesn’t satisfy the required quantity of the issue-to, some indication will be printed in the issues list so that you will know the insufficient quantity.
When a part you were unable to issue because of the stock insufficiency has been delivered, it will automatically be shown on the next issues list. Thus, you will be free from the extra, cumbersome management.
Product Goods Issue Instructions, Actual Results
With both the Customer Order and Sales Management Option and the Issues Management Option, you can manage product goods issue instructions and actual results from the product warehouse to the shipping workplace before shipping the product.
The mfg. lead-time is taken into consideration for internal processes to make a schedule for products in the MRP calculations, but you make arrangements for the required quantity of parts and materials using the MRP calculations, and for the instructions for internal processes, the work instruction can be given to the preceding process step according the timing of a group leader on the factory floor who’s responsible for producing products.
The process step to follow brings the required quantity from the stock of the preceding process step, which in turn produces the portion that has been used and become insufficient. Thus, you can achieve a behavior like so called “kanban.”
Use the Schedule Detail Manual Entry form or the Shop Floor Control Option for the instruction to the preceding process step
In the case of the discrete production, since they make a different product for each customer’s order, their application is not the kind like they would put the master tables in order beforehand and perform the uniform processing like the repetitive production. Because of that, the systems for the production control, where you had to put the master tables in order beforehand, used to be very hard to use. In order to solve these problems, TPiCS has strengthened its function to accommodate various operation methods. Even for individual production, not all products are individually designed, but common parts and repair parts may be arranged by repetitive manufacturing function and incorporated into one-item production configuration. It is possible to use repetitive production function depending on the product, or to manage mixed fine-grained management using the Mfg. No. Control.
This is a function with the assumption of a case where you will operate the system without predefining any master tables due to the “one-time-only production” because the product specification will change in each customer order.
・ By a very high operability, you can arrange while registering work and parts to be used each time.
・ You can copy a similar mfg. no. in the past and change it to make a new one for use.
・ The drawings get released like an early summer rain and you can arrange things, starting with what you need and it’s possible among them.
・ If patterning is possible to some degree, you can use it as the base to which you can add some modifications.
・ You can perform addition, modification and deletion seamlessly due to the engineering change by working together with the “Structure Information Conversion Option” and reflect them in the arrangements promptly.
・ You can use the general-purpose units and parts that have repeatability.
・ You can issue the “Quotation” to your customer.
・ You can issue the “Quotation Request Slip” to your supplier and a transaction that conforms to the Subcontract Act is possible. (The competitive quotations are also possible.)
・ You can manage a part that has become unnecessary because of the engineering change or something, and let other projects use it.
・ This option requires that you purchase the “Mfg. No. Control system.”
“Product structure information” and “change information” of the design are read as structure information in the CSV file from the parts table managed by CAD and Microsoft Excel, and are reflected in the production information of TPiCS. Coordinate processing can be done with one data, so design changes will be reflected on production thoroughly and quickly.
・ You can register the work, such as supply and outsourcing processing, that doesn’t exist in the engineering BOM in the manufacturing BOM.
・ Even design changes made from the design BOM to the manufacturing BOM can be quickly reflected in the arrangement.
・ This option displays a portion of engineering change with the status or in color so that any omission of the processing can be protected.
・ If you use this option in combination with the One-item Production Option, you can reflect the engineering change in the arrangement data seamlessly.
Taking advantage of the CAD data
Because the customer’s needs have diversified and the life cycle of the merchandise has also shortened, it has become more important than ever even for the discrete production to shorten the cycle of customer order, design and production.
So, in order to make things in rapid cycle, you’ve come up with an idea to make arrangements for the production using the engineering information. But the structure information of the products the engineers think of (E-BOM) and the structure information the people of the mfg. department think of (M-BOM) are different often times, and it is general that the E-BOM gets changed to the structure information for the production with an interpretation of human being added. Then, if there’s an engineering change, it becomes impossible to change it directly in the system and reflect it in the arrangements. That’s why the human being has reflected engineering changes by comparing the E-BOM and the M-BOM one by one with his eyes.
But if there’s an engineering change and you use the “Structure Information Conversion Option” of TPiCS, it will be possible by just clicking the button a several times to find out something unnecessary or something that needs an additional arrangement from the data that have already been arranged (purchased) to create a cancel order and to make an order for additional arrangement even if there’s a difference between the two of the structure information. With this function, the production control business for the discrete production should be very easy.
This adjusts the schedules of multiple parts or products that are designated as the same group so that they will always be made at the same time.
・ If you were to process a part the right side of which is different from the left and both are made at the same time in one mold, for example, you would always have to produce each of them with the same quantity at the same time regardless of the ordered quantity. In this case, you will be able to make a schedule for them with the same quantity each at the same time in the MRP calculations.
・ In the case of having a by-product generated, you can let the schedules of multiple products created at the same time according to a specified ratio.
・ When you change a daily schedule with a drag-and-drop to the production schedule table, you will always be able to change daily schedules all together for the items that are designated as the set production group, and reflect the results in the Gantt Chart By Mfg. Sector at the same time.
With this option, you can produce things for sales orders to be shipped at the end of the month ahead of schedule, and make a production schedule taking into account the load on the ability of the bottleneck process.You can perform the leveling process that represents the “equally-allocated production” where the daily production is equally allocated with respect to the total number of one week.
・The amount of work and the load factor are aggregated based on the calculation results of the parent hierarchy for each hierarchical level of the structure in the MRP calculations. If there is something where the load factor is more than the set value, the appropriate schedule will be moved to the front and rear.
・The move will target only the undetermined schedule.
・The MRP calculations will continue based on the schedule after leveling for child parts under it.
・The processing of “front-loading” and “back-loading” is possible.
・For each production line, you can set the necessity and the reference load factor of leveling.
・You will be able to set the items of interest in the “leveling priority” of the Item Master.
・The processing of “equally-allocated production” will also be calculated for each parent-child level.
A schedule to produce evenly will be created for each week and item after the inventory allocation and the going-back calculation of lead-times. The calculation will be performed for the items of low-volume production so that as much schedule as possible will be made at the beginning of the week.
It is an option that you can trace the actual results of assembly and processing of manufacturing from the product lot name shipped and Procured raw materials and lot name of parts.
In addition to tracking raw materials from the product, you can also track the ship-to party from the lot name of the raw material in which the problem was found.
It can support the lot traceability required by ISO 9000, PL Act, Pharmaceutical Affairs Law, etc.
You can also manage the expiration date of raw materials and inventory of work in progress
・You are going to enter the lot numbers for raw materials if necessary (setting) at the time of receiving them. (Can be designated as mandatory.)
・You can register the internal lot numbers and their association with the lot numbers for the raw materials that have been used at the time of entering the actual results for internal processing.
If there’s something that needs the traceability control among the raw materials to be used, TPiCS automatically allocates that in “FIFO” first. Afterward, since a window that lets you confirm the allocated raw materials opens automatically, you can correct them there as needed.
・One product or process can use a raw material that contains multiple lots and one raw material can be used by multiple products or processes. That is, handling many-to-many relationship is possible.
・You can also manage all the moves within the factory such as issuing partially and returning to the warehouse after raw materials in stock.
・Since you get to know the price purchased of the raw materials that have been used, and the operator and the hours worked when there was work, you can figure out the net cost of each of the lots produced using the “Cost By Lot” form.
・For raw materials and goods in-process requiring “expiration date management”, you can print a list of items that are about to expire and discard them all at once.
・You can perform the MRP calculations taking into consideration the expiration date after the completion of the product and after receipt of intermediate products and raw materials used.
・You can instruct about the “raw materials to be used” on the work order form. The instructed raw materials are temporarily allocated and then withdrawn automatically at the Actual Completion Results Entry for the parent. You can also change them halfway.
It is an option to record approval of high purchase order and all table changes, and to prevent fraudulent work processing.
・You can have a correction history for all tables written out to the dedicated table.
・You can target only the data a “person with the purchasing approval authority” has approved in the issuance of the purchase order form.
A “person with the purchasing approval authority” can be discriminated by a special setting.
The “Approver,” the “Date and Time of Approval” and the “Approval Key (cipher)” are written in the approved data, and when you change the content of purchase order after approval, the approval will be invalid.
・You can record long operation logs.
This is the system to perform the process control for the factory floor and we’d like those who wish in the following way to use:
“I want to put out the sound schedule with a pile of load since the people on the factory floor complain if I cannot manage the load when I give instructions to them.”
“I have no control over the people on the factory floor because they are doing their way. I want to manage them somehow using the computer.”
“Time of setup is different by the order in which to produce. I want to make a schedule where time-consuming setup is as little as possible.”
“There are multiple machines at each process step and the ability is a little different from machine to another. We have things we can make and we can’t make depending on the product we are going to make. In the situation like this, I want to make a plan that is as efficient as possible.”
“Each time an inquiry about the delivery date comes from our customers, I can’t give them an answer without going to the factory floor. I wish I could tell that by looking at the screen of the computer.”
・You will see a list of work for today and tomorrow on the screen of the foreman or group leader of the factory floor, or the person in charge of the shipping field. (It’s important to limit the list to 2 to 3 days worth of work).
・When the office changes the schedule, the change is reflected in everybody’s screen instantly. Through the screen, something where necessary parts have not been prepared, something where the preceding process step has not been completed, and something that can be started at any time will be displayed in such a way that you can understand them at a glance.
Since you can display the screen by sorting data by priority order, you can begin with a rush work.
When you press the Preceding Process button in the data of possible-to-start, child parts of what are missing at which step and what’s happening to that schedule will be displayed in the window.
・You can demonstrate the daily production level (quota) apart from the results of the MRP calculations. This allows you to hold the required level of leveling of production schedule.
・Press the Start button after determining the work to do next from that screen. When you are finished, press the Register button to be able to register the actual results.
・When you press the Start button, you can even tell from the process step to follow what time the preceding process step started.
・When you register the actual results, that work will be gone from the Instruct A Schedule screen.
In other words, it will stay on the screen until you register the actual results.
・Since it’s possible to use different colors by the work and working methods when you display the work that must be done, you can think of the order of efficient work in consideration of the setup by choosing the work with a similar color.
・When you register the actual results in the screen of the Shop Floor Control, it will be reflected in the stock quantity, etc. of TPiCS in the office at the same time.
・The actual results entered at the preceding process step will be reflected in the Signal To Start screen of the process step to follow right away and the display in red on the screen will be gone.
・In the evening you can print the daily report and the not-yet-done list for today using a PC in the office without bothering anybody.
The Shop Floor Control Option is not for directly responding to the needs that emerge on the surface like this, but is intended to achieve the “true management” soil improvement-wise, and is the system for the factory floor to be able to make correct judgments, not to enter the actual results for the purpose of collecting them, by solving the problem that exists behind it or removing clutter on the way to that problem.
This is an option that allows you to change the parts, materials, and intermediate units used for production from the standard structures even after the production schedule is created. To change the item used after finalizing the production schedule, you need to maintain plan and actual results data. The Alternative Production option makes the procedure easier and allow for more flexibility in temporarily changing the raw materials used.
For example, it is suitable for cases where you replace parts that are not on time for the specified delivery date with available alternatives and produce, or you use up the raw materials first which are going to be wasted because the expiration date is near instead of the raw materials normally used.
Switching between items can be done at the planning stage or at the time of entering actual results after work. This makes it possible to deal with both cases where the change of the used item is confirmed before production and cases where the change is determined by on-site judgment during the work.
Also, you can replace the entire quantity or a partial quantity with a substitute for the originally planned quantity.
It is an option for performing automatic linking in both directions by importing data of another system into TPiCS and writing processing done by TPiCS to a linkage table.
For example, the Actual Receiving Results data, the Issues data, and the Actual Work Results data registered at the handy terminal are automatically imported by TPiCS to the Transaction Import table and can be processed in the same way as entered from the TPiCS form.
In addition, a table for transfer is prepared for the Actual Shipping Results data entered into TPiCS in conjunction with ERP and Sales Management System, data is automatically added to the Transaction Export table at the same time as data entry, and you can grasp updated data of TPiCS. When you check to prevent double data transfer, it may be necessary to update TPiCS data. At this time, if you update directly to the Actual Shipping Results table, you will need to check the effect on TPiCS processing, but if it is the Transaction Export table, since only data is added from TPiCS, it is possible to update the transferred items easily.
・Import of the EDI data and the Forecast data with customers
・Coordination with production scheduler that adjusts machine production on a time basis
・Import of the Actual Results data collected from the machining center
・Coordination with POP terminals for collecting actual results, handy terminals and smart devices. Linkage with actual receiving results and actual work results using RFID
・Coordination with the Cost Management System that distributed and aggregated overhead costs
・Linkage with ERP, the Sales Management System, and the Accounting System
・Linkage with the workflow system for purchase order approval
You can automatically create delivery schedule from product shipment to delivery destination and issue the loading slip.
When you select the loadable items on the basis of the shipping schedule, the load weight limit and volume restriction of a truck is created from the weight and volume of the product after packing. In addition, a delivery plan that automatically distributes the loaded items for each delivery area registered in the master is created.
Please use it in conjunction with the Customer Order and Sales Management Option.
The SCM Option is an option to strongly cooperate with suppliers and cooperating companies requesting production to realize production that responds promptly to fluctuations in forecasting order finalization and a sudden, irregular sales order from customers.
You can send purchase order and forecasting order information to the business partner from the supply chain host, and at a cooperating company you will receive it using the supply chain terminal. In addition to simply sending and receiving order
information, you can also reply whether or not to deliver according to the designated delivery date from a cooperating company. If it is impossible, you can also reply with partial deliveries. Since sending and receiving is a mechanism of e-mail, it can be used if dedicated e-mail address can be prepared.
In order to realize fast cycle production, as internal improvement progresses, it will become necessary to have the purchase order lead-time of the cooperating company shortened in order to further improve. At this time it is difficult in one way, and when the production of the cooperating company can not really make it in time, you will make the purchase order lead-time that is established on trust relationship by receiving this. Since TPiCS has a concept of buffer called basic stock, partial delivery is alright if it can be covered with this. If it can not be covered, it can be displayed in the journal and you can judge whether you want to ask the customer to change the delivery date. It is easy if you follow the exchange of one purchase order data, but you must solve the problem in a large amount of data that changes from day to day, such as the situation of cooperating companies, the situation inside the company, and the change of the the product plan using the same parts.
Although you can use the supply chain terminal for free, upgrading to TPiCS seamlessly connects from the supply chain terminal to sales order and MRP calculations and demonstrates its true value.
When your customer asks you for the delivery date reply and if you confirm the inventory and the on-site progress and the answer is given after several days, the situation of the customer may change. In the Delivery Date Reply Option, of course, you can answer “Yes, possible” or “No, impossible” according to the requested delivery date, but even if it can not be done, you can respond schedules that can be handled by partial deliveries.
Calculated inventory of the required day is determined from the sales order and shipment plan, the production plan, and the remaining quantity of lots of the production plan in order from the product level. In the case of shortage, the calculated inventory is examined by drawing child parts to be used and intermediate units, and finally the calculated inventory of the end member is examined. In the case where the calculated inventory of the parts is insufficient, conversely this time, the parent’s plan is adjusted from the plan that keeps the purchase order lead-time, the schedule of the intermediate unit and the production schedule of the product are determined and the deadlines that can be handled to customers are calculated.
You can specify only the quantity and can answer which deadline you can deal with.
After calculation, you can create Sales Order data and Schedule Detail data directly from the Reply Request data and the Reply Detail data, and you can reflect it in the next delivery date reply calculation.
After shipping the product to the customer, the Service Part Management Option is an option that performs:
①Guide on the end of useful life of service parts and maintenance parts,
②Creation and arrangements of forecasting plans for applicable parts, and that makes it possible to deliver to customers immediately without deranging the production schedule of the product by receiving sales orders of the service parts by regularly urging parts exchange instead of the customer placing a purchase order for repair parts in a hurry after breakdown.
Concretely speaking, you will manage parts that will need to be replaced within a few years from the shipped products as service parts and you can confirm the replacement to the customer at the timing when the service parts are needed after several years from the shipped actual results and manage the additional order only for the service parts.