GENERAL INTRODUCTION TPiCS – an advanced and comprehensive production management system – was developed at TPiCS Research Institute, headquartered in Tokyo, Japan. Currently, more than 1900 businesses around the world are using this system. The system integrates multiple languages and is available in server and cloud versions.
MFG. NO. SYSTEM OF F-MRP TPiCS can accommodate and manage the mix by using f-MRP functionality for repetitive production and mfg. no. control system for make-to-order production. After closing the order, you need to prepare the finished product and intermediate products; you can specify how to manage general materials by finished product unit, intermediate unit, and material under f-MRP management.
REPEAT PRODUCTION SYSTEM TPiCS is suitable for the production of highly repeatable and common materials; respond to changes in orders and forecast; limiting the impact on finished product production, intermediate processes and material mobilization.
PRODUCTION NUMBER MANAGEMENT SYSTEM TPiCS is suitable for high mix – low volume production with little change of plan. In addition, users can also easily grasp the relationship between each instruction and the order thanks to the plan linked by production numbers from the finished product process to the intermediate process, the first process and the materials preparation process.
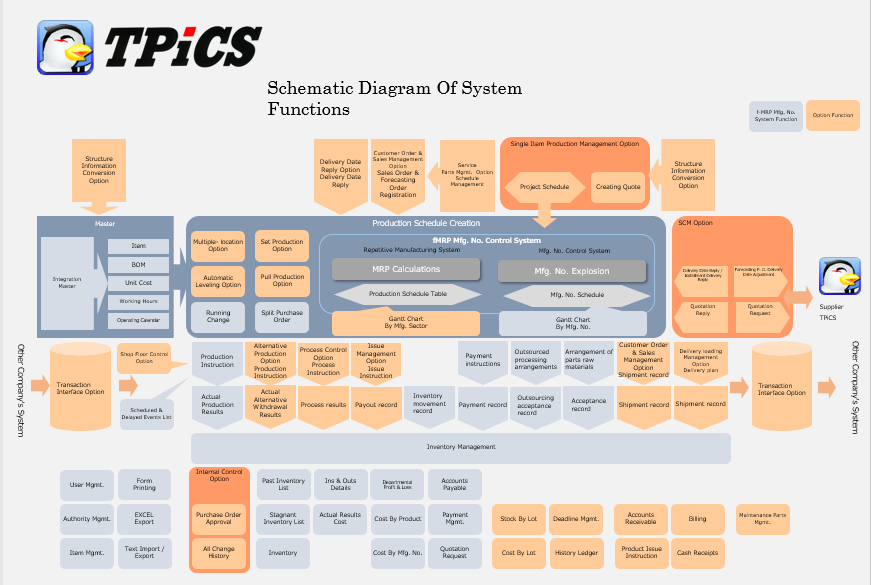
FUNCTION TO CREATE THE PRODUCTION SCHEDULE(f-MRP) (REPETITIVE PRODUCTION SYSTEM)
– TPiCS realizes the “prompt, inexpensive, responsive, but stable production” through its own f-MRP function. – Using the sales plan and the production schedule for products as a starting point, TPiCS automatically creates the schedules for production and arrangements up to intermediate units and end raw materials according to the bill of materials, the mfg. lead-time, the lot size, etc.
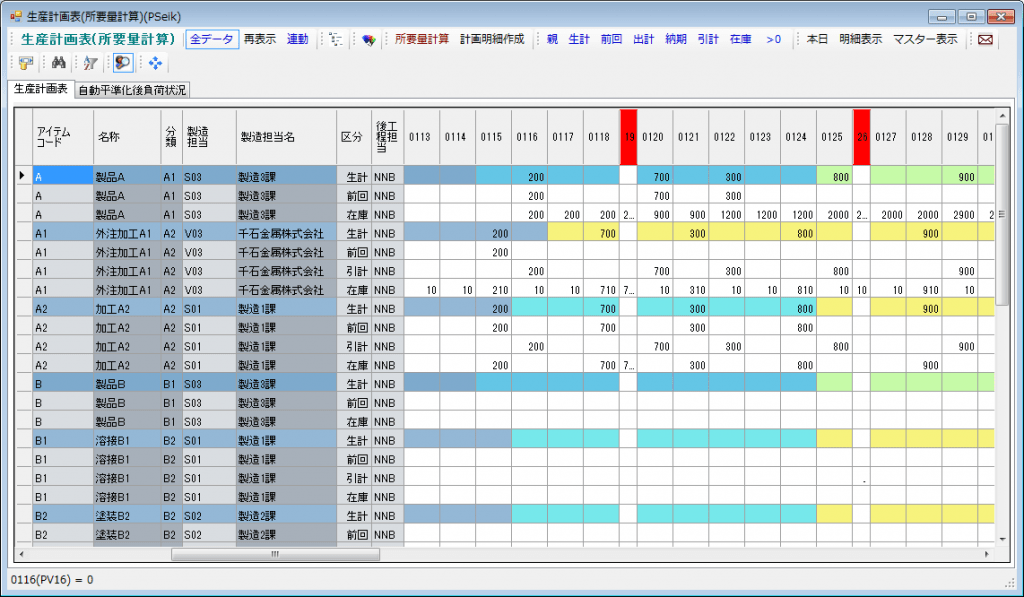
When you use the Customer Order & Sales Management Option, it’s also possible to operate the system to make the production schedule according to the customer order and forecasting information, and to automatically make the production schedule where the production is in time for the shipment, which is a starting point, in the environment where there’s no customer order or forecasting information like responding to short-term or immediate deliveries, and make arrangements for intermediate processes, parts and materials from there. – When calculating the MRP, ordered parts, supplier’s delivery delays and production delays will be added and subtracted from the current inventory, and a production plan will be created. Users can register multiple inventories, combine multiple inventories for calculation, and set up a inventory that is not subject to calculation. – TPiCS makes the production schedule by adding something already purchased, something delayed in supplier’s delivery and something delayed in operation to the current stock at the time of the MRP calculations. Multiple storage locations can be registered, and it’s also possible to combine them for the calculation and to set them to the storage location not subject to the calculation. – It’s possible to register operating calendars. With them, you can make the production schedule for the initial process in accordance with the calendar of your outsourcing processing company, and, when you are using the Customer Order & Sales Management Option, you can make the shipping and production schedules in accordance with the operating calendars of your customers.
Journaling function (Warning information)
In the MRP calculations, a schedule change one ought to pay attention to like “falling below the purchasing lead-time”, which is derived from various situation changes such as a new customer order, a delivery date change, a change in quantity of customer order. The intermediate processes to the “Order Leadtime Split” are shown in the journal.
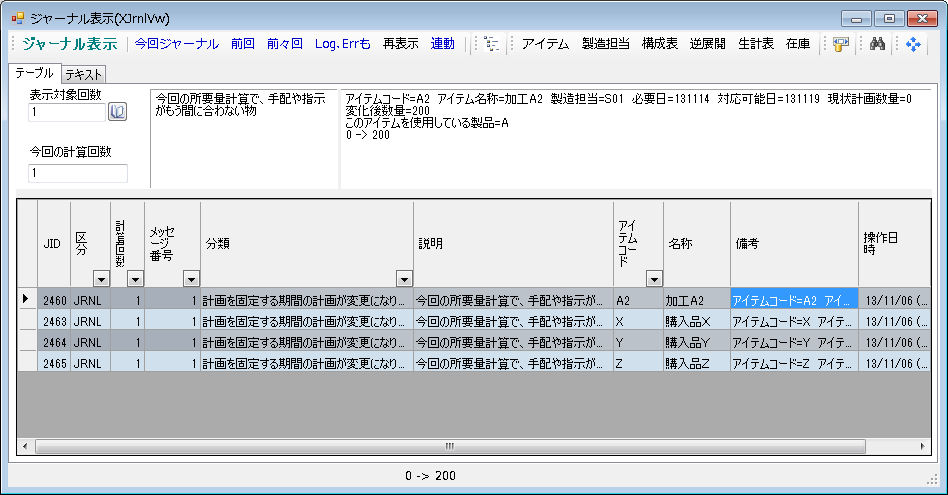
From the journal, the system can connect to the production schedule board and display the information, and the user can adjust the production schedule, confirm the supplier’s information, confirm the status on the component or on the master.
Running change function
All you need to do is register old and new codes for a part in the Engineering Change Master, and that will automatically switch the old code to the new one for the purchase by calculating when to consume the stock that currently exists and what has been on order. It automatically responds to changes in the production schedule and inventory. When the actual results for the parent are entered, the minus (withdrawal) of the used child parts is also automatically switched. You can also directly specify the part switch date. (Bill Of Materials) ・ Gantt Chart By Mfg. Sector Option As a result of the MRP calculations, you can check the workload of the manufacturing department from the created production schedule and adjust the plan on the Gantt Chart By Mfg. Sector. ・ Automatic Leveling Option It’s possible to perform the automatic allocation by the production capacity, the standard operating time, the quantity and the allocation priority of the work center. ・ Multiple-location Option It is possible to set up a production schedule in which products and units are automatically split by ratio at multiple manufacturing locations, or to produce in-house usually, but if the production limit is exceeded, partially outsource production to cooperating company. You can also make a production schedule that arbitrarily allocates manufacturing locations.
FUNCTION TO CREATE THE PRODUCTION SCHEDULE (Mfg. No. System of f-MRP Mfg. No. Schedule)
The Mfg. No. Control of TPiCS allows for the following 3 control methods:
- B-Seiban: This is a basic method. The arrangement schedules that are connected to product, intermediate unit, material and part through the mfg. no. will be created from the mfg. no. schedule according to the product structure through the mfg. no. explosion. You can change the product structure for each mfg. no. schedule.
- S-Seiban: This is the mfg. no. control of precedent arrangements. You can arrange and produce the intermediate unit with the preceding mfg. no. attached, and allocate it to the final mfg. no. to produce the product.
- F-Seiban: This is the mfg. no. control of f-MRP. It is a management method that calculates the required amount by f-MRP, which is flexible to fluctuations in demand, and links the created Schedule Detail with mfg. nos.
Structure Change Function
Two ways of changing the product structure by mfg. no. are prepared:
- Way to use the option code
- Way to change the structure after the mfg. no. explosion
Cost Aggregation by Mfg. No. Function
・You can calculate unfinished work as the predetermined cost and manage budget and actual amounts in contradistinction to the standard cost. ・You can include a part that was calculated by f-MRP as well in the Cost By Mfg. No.
Gantt Chart By Mfg. No. Display Function
– You can display child parts that have the association with the mfg. no. and the progress status of each process. – You can tell at a glance if the preceding process is finished, or if inventory is available for f-MRP parts, and consequently whether or not it’s possible to start now.
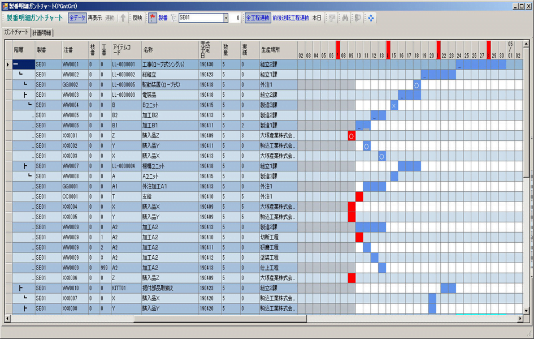
– You can change the plan date by drag & drop. – You can issue change slips for changes, and if linked with the SCM option, you can automatically send the changes by e-mail to parts suppliers and outsourcing companies.
MIXED MANAGEMENT OF f-MRP AND THE MFG. NO. CONTROL
You can specify whether you’ll go with f-MRP or the Mfg. No. Control by item in TPiCS. By this, for parts and materials that are too late to be exploded for mfg. nos. and be arranged after the customer orders come, you can make arrangements based on the forecasting orders using f-MRP that is tolerant of changes. And for intermediate units and products, you can issue mfg. orders with the final mfg. nos.
FORM ISSUING FUNCTION
WORK ORDER FORM, PURCHASE ORDER FORM, OUTSOURCING ORDER FORM, TRANSFER (SUPPLY) ORDER FORM This allows you to issue orders based on the MRP calculations, the mfg. no. explosion and the manual entry. SETTING THE LEAST EXPENSIVE SUPPLIER AUTOMATICALLY You register different unit prices in the Unit Cost Master depending on the supplier, time, quantity, and urgency, and when creating the Schedule Detail, TPiCS can look at the time, quantity, etc., search for the cheapest supplier that meets the conditions, set it in the Schedule Detail and issue a purchase order form. PURCHASING WITH SUPPLIER’S PART NO You can purchase using supplier’s part no. (catalog no., etc.) PARALLEL PURCHASE You can issue purchase orders that have been split according to the ratio to multiple suppliers. Also, if the quantity exceeds the upper limit, you can purchase the exceeded portion to other suppliers. E-MAIL TRANSMISSION The purchase order by e-mail is possible. FORM DESIGN CHANGE The form design created by Excel is prepared, the Excel form design is displayed with the Print button, the data written from TPiCS is read and automatically printed. The design includes a one-item-per-page form suitable for work instructions, a work instruction with child parts to be used, a multiple-items-per-page form suitable for purchase order form, etc. and can be adjusted with Excel function. You can also change and add design according to the paper.
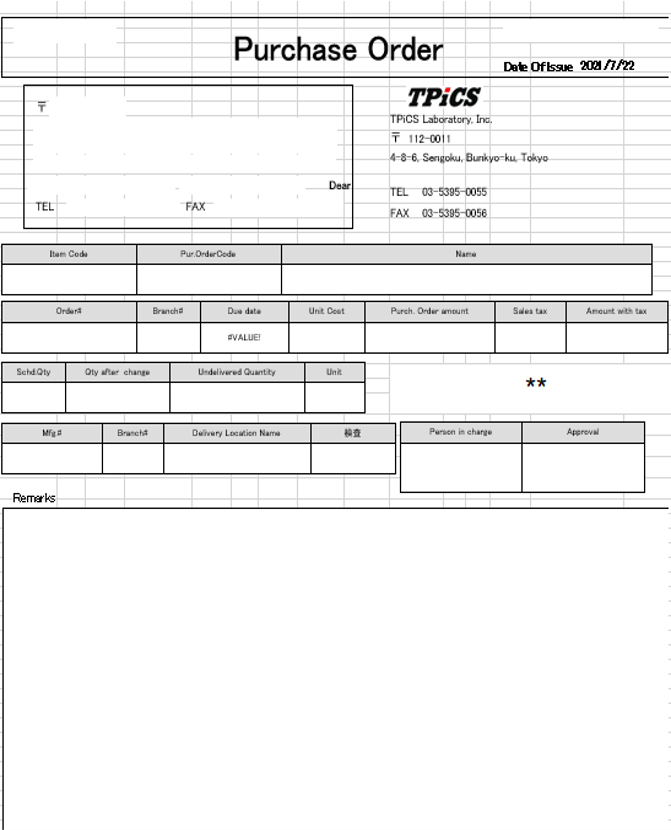
Upload Image...
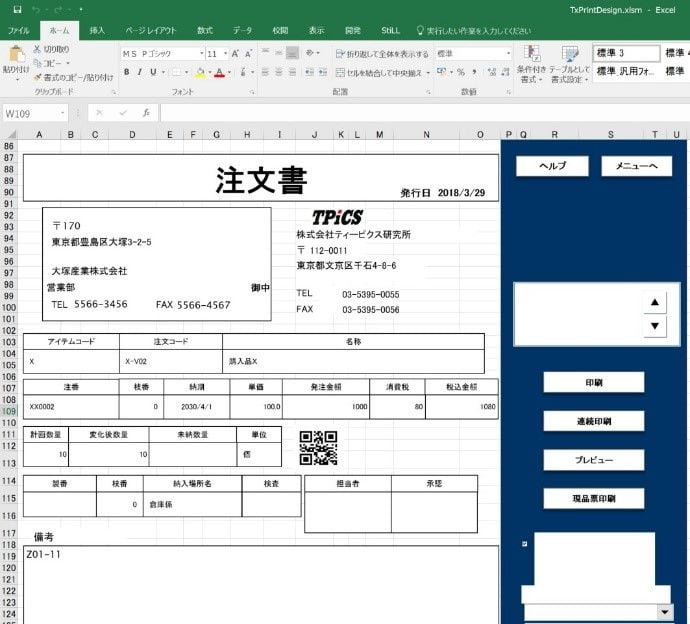
WRITING LOT NOS. CLEARLY FOR RAW MATERIALS TO BE USED (MFG. TRACEABILITY OPTION) In the work order, you can specify the lot number of the raw materials used. IDENTIFICATION TAG At the same time as the work order form, the outsourcing order form, etc., you can print the required number of identification tags according to the setting of quantity of contents. ISSUANCE OF THE DELAYED EVENT LIST You can also issue the delayed purchase order list and work order list, but instead of responding after delivery time delay, in order to prevent delays in delivery, for example, next week, it can be issued for each supplier as a list of schedule of acceptance. QUOTATION REQUEST You can issue the Quotation Request Form for parts with no unit price. With this function, you can create a purchase order form compliant with the Subcontract Act. SUPPORTED EXCEL Microsoft Excel 2010, Microsoft Excel 2013, Microsoft Excel 2016, Microsoft Excel 2019, Microsoft 365 (desktop application Excel only)
ACTUAL RESULTS MANAGEMENT
ACTUAL PRODUCTION RESULTS ENTRY hen you enter the actual results for an intermediate unit that’s manufactured using parts and materials, inventory of the intermediate unit increases and that of the material decreases because of being automatically withdrawn. For the withdrawal, a suitable way varies depending on the production method for parts and materials. For example, in the actual assembly results when the completed quantity is small relative to the planned quantity, parts are put in according to the planned quantity, but in the case of disposal due to damages, it is necessary to withdraw by the quantity of inputs.
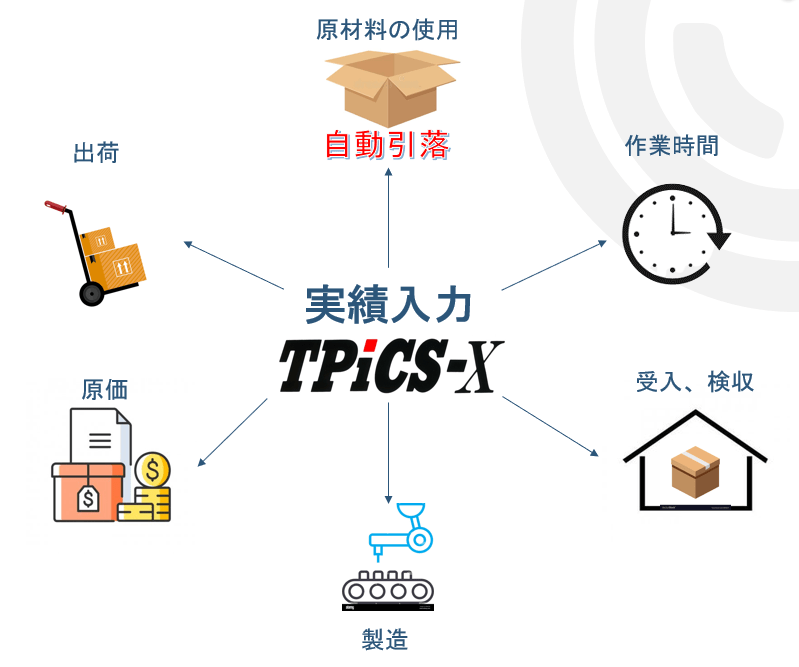
But in the case of partial completion due to production delay, it is good to withdraw the same amount as the completed quantity. Also, if it is a liquid product, you may want to adjust the withdrawal amount each time you enter actual results. Such a withdrawal method can be set for each management point such as parts, intermediate unit, product, etc. You can enter the actual results time for each operator, work party, machine and process, and summarize it by each of these elements. ENTERING THE HOURS WORKED OF ACTUAL RESULTS You can enter the quantity in real time for the next process in the Actual Results Entry, and enter the hours worked of actual results on the dedicated form later. It’s also possible to distribute the total of hours worked of each work party to multiple actual work results, and to automatically set it as each actual results time. ACTUAL RECEIVING RESULTS, ACTUAL ACCEPTANCE RESULTS You can also enter two levels of actual results, actual receiving results of receipt confirmation and actual acceptance results to be inspected and subject to payment. It is displayed on the accounts payable according to the actual acceptance results. ACTUAL RESULTS COST You can take over the unit price purchased of the Purchase data to the actual results and change the unit price purchased of actual results at the time of entering the actual results. Also, in the actual work results entry, the hours worked of actual results and the processing cost rate are reflected in the actual results cost. Inventory can be evaluated using the real-time moving average method, monthly moving average method (monthly gross average method), final unit price method, gross average method, or lower-of-cost-or-market method. ENTERING IN BLOCK If you can produce as planned everyday, it’s natural that you want to save time for the entry. In this case, you can automatically set the temporary actual results quantity in the schedules that are scheduled to be completed today, and enter only the Schedule Detail for which you could not produce as planned. Thus, you can enter the actual results in block. ENTERING THE LOT NAME (MFG. TRACEABILITY OPTION) When you are required to enter a lot no. at the time of receiving something because, for example, it’s an important raw material, the Lot Name Required is the setting for you. You can specify which raw material (lot no.) you used at the time of entering the actual production results, and you can go back to view that data any time you want. It’s possible to record a mfg. history as necessary from the point in time of receiving to that of production completion (shipment).
INVENTORY MANAGEMENT
INVENTORY LIST Inventory can be managed by actual receiving results, actual production results, automatic withdrawals due to actual results of the first process, inventory transfers, and transfers between warehouses due to issues. In addition, it is possible to grasp inventory value, the number of ins and outs for the current month, the final withdrawal date, the final goods receipt date, etc. for each item such as raw material, intermediate unit, supply-to, product, etc.
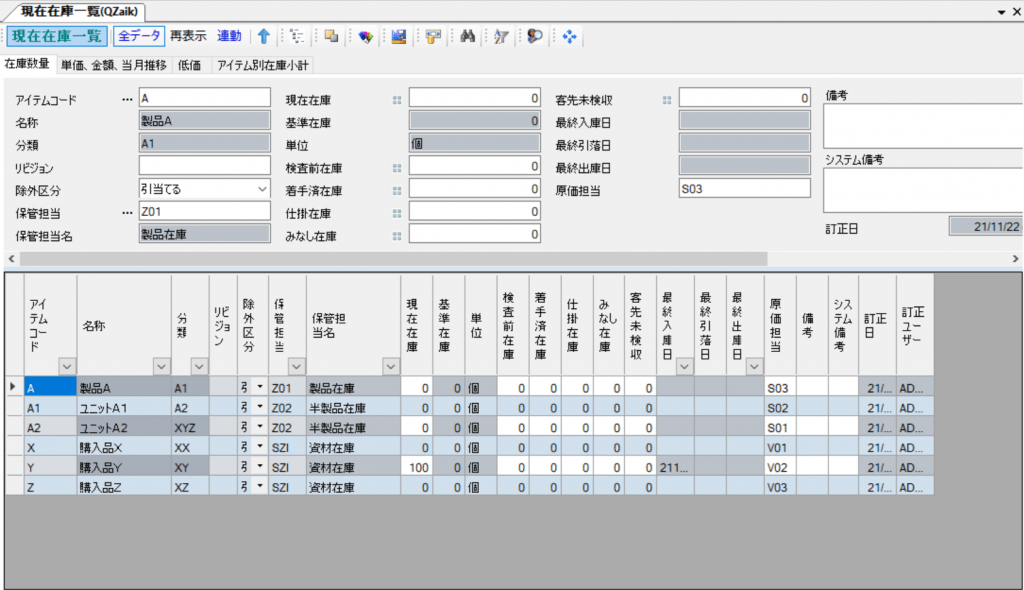
You can manage multiple inventory locations by specifying the goods receipt location at the time of goods receipt, and specifying the goods issue location at the time of goods issue. You can use the Traceability Control Option to manage in-process inventory for each goods receipt lot. You can display and print parts that were not used for a specified period in “Stagnant Inventory List.” STOCKTAKING You adjust the “current inventory” to the inventory actual quantity that exists at the storage location by performing stocktaking processing at the end of the period or the end of the month. TPiCS also supports temporary stocktaking and cycle counting, which is not a simultaneous stocktaking but a partial inventory. Since Actual Inventory Results data for inventory differences are created when inventory differences are made, it is easy to aggregate how much the inventory difference is.
FUNCTION OF THE QUANTITY CONVERSION
For the planned quantity of the production schedule table, the planned quantity can be converted according to the unit displayed on the slip, the display of the Inventory List can be converted, the Bill Of Materials can be converted, and the unit can be changed for display for each product, intermediate unit and member. For example, you can calculate the purchase order quantity of liquid material as 400 liters, and when you place an order, you can convert it to 2 cans per drum can (200 liters) unit. Conversion can then be returned at the time of 2 canned actual goods receipt results, and it can be reflected to stock at 400 liters.
COST CONTROL COST SUMMARY TABLE BY PRODUCT How much it cost to produce each item this month is aggregated and displayed based on the Actual Results data. COST BY DEAPRTMENT, SUMMARY TABLE OF PROFIT & LOSS Considering what the following process has used the sales, the profit and loss by department is aggregated and displayed.
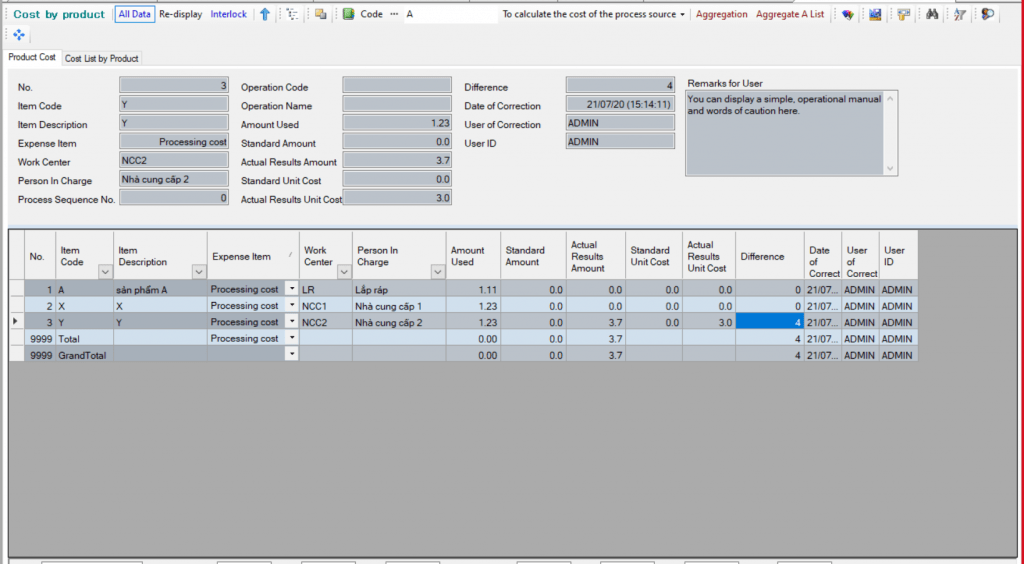
COST SUMMARY TABLE BY MFG. NO. (F-MRP MFG. NO., MFG. NO. CONTROL SYSTEM) You can view costs by contrasting the standard cost with the forecast for actual results including the unfinished predetermined cost. FUNCTION OF THE RE-CALCULATION OF THE ACTUAL RESULTS UNIT COST If you calculate the actual results unit cost using the moving-average method, you can re-calculate it by reprocessing all the Actual Results data in the order of their date, starting with the value of the beginning of the month. SUPPLY MANAGEMENT Managing paid and free supplies is possible.
AUTHORITY MANAGERMENT, USER MANAGERMENT ROLE MANAGEMENT (AUTHORITY MANAGEMENT) You can freely set the operable range of the business person like “The person in charge of planning operations can update all Item Master’s records and the Bill Of Materials and execute the MRP calculations.” and “The entry person of actual acceptance results can only enter actual material acceptance results.”
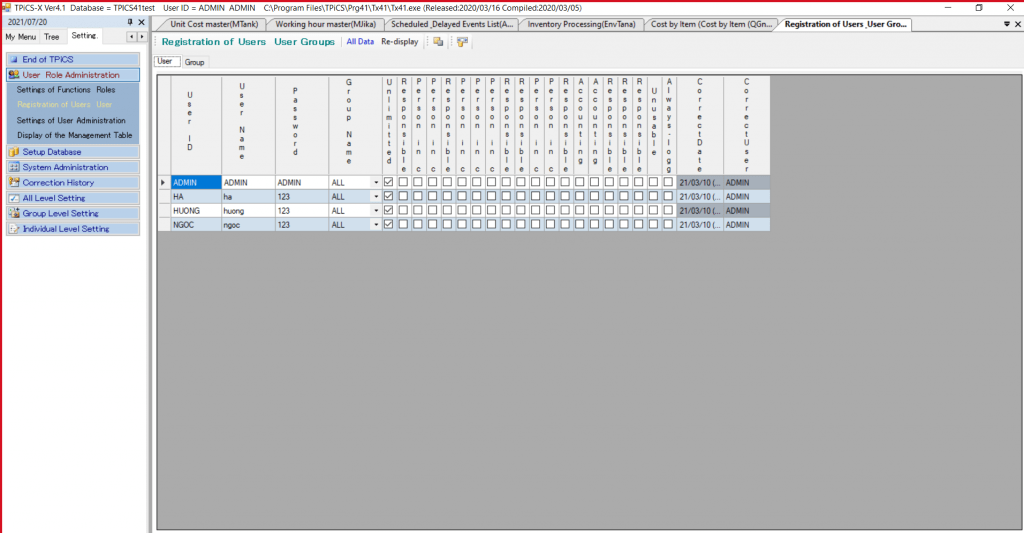
USER MANAGEMENT You can set up a role for the user. A combined setting like the planning operation and the purchasing operation, and a grouped setting containing multiple users are possible. It’s also possible to manage using the login user of Windows.
MASTER MAINTENANCE There are many masters in the master of TPiCS such as the Item Master, where you register parts, raw materials, products, intermediate units, partial processing consignment (plating, heat treatment, painting, assembly, etc.) to a cooperating company, the Bill Of Materials, where you build parent-child relationships of items, the Unit Cost Master, the Working Hours Master, etc. Maintenance of the master is indispensable in order to make the production schedule suitable for daily changing production.
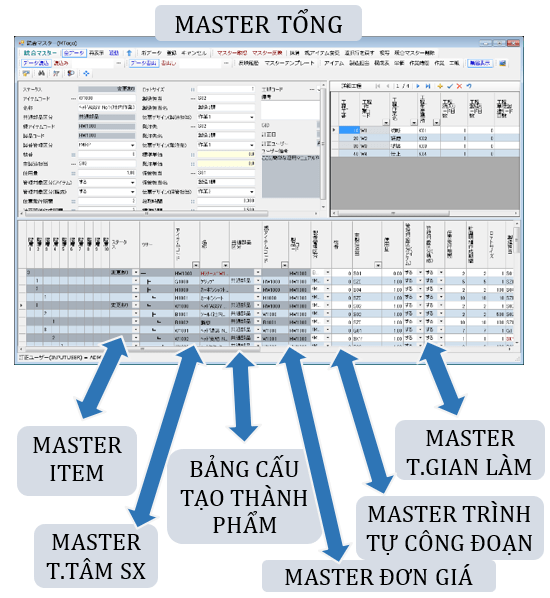
The Integration Master, which you can examine and edit at the production meeting which gathered relevant departments, is prepared as the standard function while confirming the overall picture by putting together the masters which are the main of these management. When creating a new product, you will create a product structure with the Integration Master from the BOM, and items that have already been registered can be used as common items with the Item Master data displayed. If you use the Integration Master in this way, you can build a Master with BOM image of each product and reflect it on each master. You can change from either each master or Integration Master, Outlined master registration can be done from the Integration Master, and details can be done from each master for each department in charge.
ADDING USER FIELDS,ENTRY FORM DESIGN CHANGE FUNCTION You can add your own management fields to many forms such as master, Schedule Detail, actual results, etc.
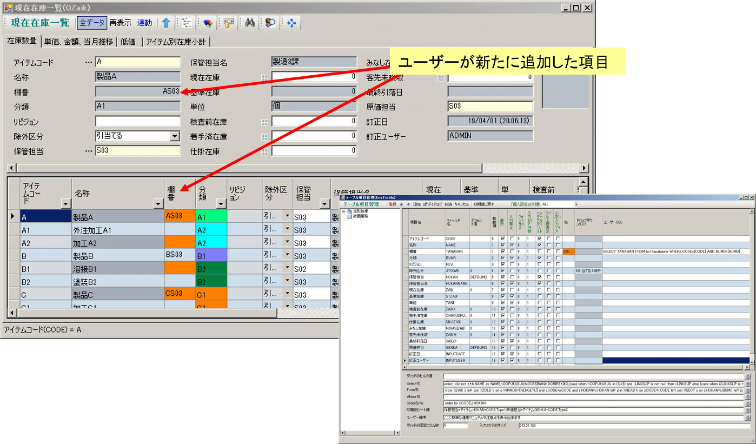
Like the existing TPiCS fields, the added user fields can be displayed in the grid and detail sections, searched, narrowed down, and entered, and data can also be selected from registered pull-down lists and entered. You can make detailed settings such as font size, back color setting, IME setting, display, hide, tab cursor order, display order, etc. You can also change the name of the grit titles of existing fields, so It can be set with the package function to the form tailored to the user. In addition, by registering the SQL statement, it is possible to refer to and display the user field set for the master in the Schedule data, circulate the value and write it in the Actual Results data, and also refer to the fields of Sales Management System of another company if it is possible to refer to them from the database server.
ACCOUNTS PAYABLE & RECEIVABLE LEDGERS ACCOUNTS PAYABLE LEDGER (ACCOUNTS PAYABLE DETAIL) When you enter the actual acceptance results, you can enter the amount purchased, the supplier, etc., and that will be reflected in the accounts payable. You can export data of the Accounts Payable Detail and the Accounts Receivable Detail according to the “import format for the journal data” of almost all the general accounting systems for the PC. ACCOUNTS RECEIVABLE LEDGER (ACCOUNTS RECEIVABLE DETAIL) – CUSTOMER ORDER & SALES MANAGEMENT OPTION The Actual Shipping Results Entry reflects the sales amount in the Accounts Receivable Detail.
PAYMENT MANAGEMENT You can aggregate the data that are subject to payment from the Actual Acceptance Results data, create a payment schedule according to the closing date and and manage the actual payment results. Since you can specify a payee different from the destination of the purchase order form, it is also possible to make the supplier of the parts a branch office and make the payee the head office of the supplier.
OPERATING CALENDAR You can register a calendar that has different holidays and operating time. There’s no limit to the number of calendars. Managing shifts like day shift and night shift is also possible. (Max. 24 shifts) You can specify the calendars to be used for factories, processes, suppliers, outsourcing companies, etc. You can set up the settings with different particle sizes, such as by day shift and night shift for this month, in a unit of days for the next month and in a unit of weeks for the month after next, in one calendar, and create a production schedule in accordance with them.
CAPABILITY CALENDAR You can set the capability of the production location that changes every day to the capability calendar. The daily production load factor can be checked with the Gantt Chart By Mfg. Sector by the capability calendar, and it is also possible to level a load in combination with the Automatic Leveling Option. Every Wednesday’s capability is lowered for planning maintenance of production equipment. It can be used for checking the number of part-time workers and workloads that change every day.
AUTOMATIC EXECUTION FUNCTION You can automatically do the same operations, for example, for the import of transaction data and the monthly processing, as you would do manually by preparing the commands for the fixed form processing as a script file. For example, you could import the Sales Order data in the lunch break everyday followed by the automatic execution of the MRP calculations, the Schedule Detail creation, and the order creation.
FUNCTION OF DATA SEARCH, FILTERING & SORTING Equal search, partial match search, leading match search, and above, below and negative searches can be done in almost all forms and items. In addition, there is a quick search function that searches as soon as you enter the search value into the keyboard, and you can display the necessary data while checking from time to time. You can narrow down by AND or OR condition under multiple narrowing conditions. You can sort by double clicking on the grid title line.
INTERFACE LINKED TO OTHER SYSTEMS TEXT IMPORT & EXPORT TEXT IMPORT & EXPORT You can import and export data of all the tables which are the master tables, the transaction data such as Schedule Detail and the already purchased data, the Inventory List and the summary data such as Cost Summary By Item and Cost Summary By Department in text file format.
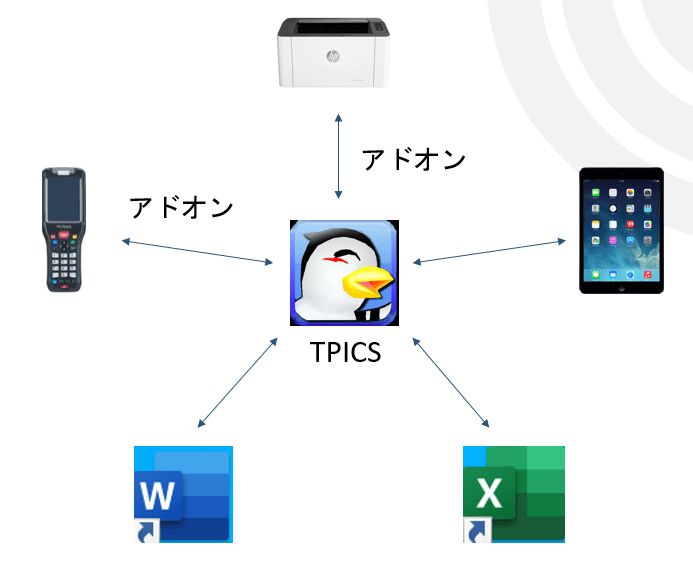
TRANSACTION DATA TEXT IMPORT The updates of related tables occur at the same time as you import the text file as well as you would operate the entry form such as Sales Order, Schedule Detail, Actual Work Results, Actual Shipping Results, Actual Issues Results and Inventory Transfer. In the case of importing the Sales Order data, the imported data will also be reflected in the production schedule table at the same time as the registration of the Sales Order data. TRANSACTION AUTOMATIC IMPORT & EXPORT (TRANSACTION INTERFACE OPTION) If you assume frequent data imports on a text file basis, it will be difficult to deal with import errors because of data inconsistencies. In the Transaction Interface Option, if an import error occurs, the error description is written in the table and the status control is performed. So, cooperation becomes easy to do. Also, it’s possible to automatically write transaction data you manipulated on the form of TPiCS to the write-out table. This allows you to perform the two-way cooperation with a third-party system.