Kyoden Precision Co., Ltd. (Japan)
A system with a good balance of decentralization and centralization is realized.
From defensive to offensive production management
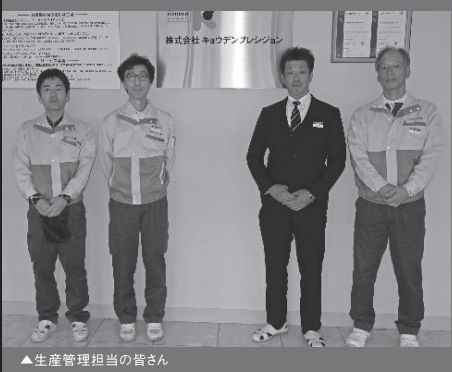
1. Situation:
Kyoden Precision has unified the production management of the three businesses that had been operated separately for many years into TPiCS. While maintaining the independence of each business, they have built a system of decentralization and concentration with a sense of unity.
- The conversion from defensive to offensive production management has improved employee motivation.
- On-site improvement is also progressing greatly.
3.Target:
In addition to improving the efficiency of individual businesses, they will make full use of their production management system to achieve their company-wide goal of providing a completely in-house one-stop solution.
Challenging the one-stop solution
Kyoden Precision Co., Ltd. (Mifuku, Izunokuni City, Shizuoka Prefecture, commonly known as KPI) is roughly divided into 3 business: press sheet metal, machining, and molding (mechanical business), printed circuit board mounting (mounting business), and assembly of unit products (unit business).
Each department also conducts its own business, but “Our goal as a company is to provide a completely in-house one-stop solution, from parts manufacturing to finished products,” said Satoru Akai, the manager of the Mifuku Factory. Including KPIs, the Kyoden Group has seven manufacturing bases in Japan and one overseas.
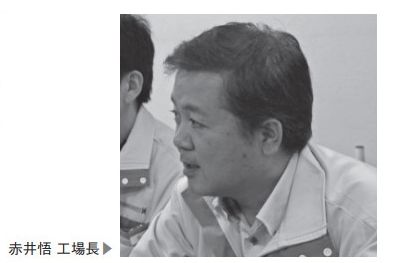
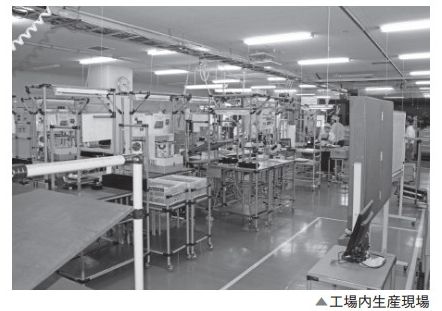
Starts with production management just for use
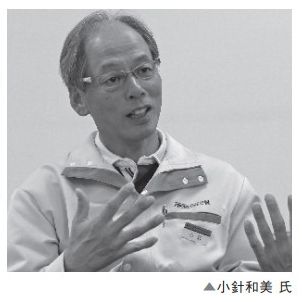
KPI’s production control system has a history of more than 30 years, including its prehistory. However, before 2000, the parent company managed the entire system, and the KPI only used that system for processing. If they made a mistake in processing, they couldn’t fix it themselves, so they had to petition the parent company to fix it. Mr. Kazumi Kobari, section chief said.
Problem: If KPI make a mistake in processing, they cannot correct it themselve, so they have to petition the parent company to fix it. ⇒ System with low degree of freedom
Since KPI’s predecessor company had repeatedly integrated, KPI’s three businesses were placed under the cover of different parent companies in the parent company, and they had no choice but to use different production management systems. However, as long as it is one company, it cannot be processed until it is finally consolidated into one. As a result, the people in charge of management of the three projects would meet on a fixed day every month and stay late to do the counting manually.
Trinity still exists
Triggered by the year 2000 problem, which was said to be a risk of computer malfunction, we petitioned the parent company to introduce a unique system for production management in the mechanical business. In addition to supplying parts internally and to the parent company, the mechanical business is also involved in parts processing for external customers, so “It was difficult to respond only with the management system provided by the parent company” – Mr. Tetsuya Sano (Section manager of the mechanical business).
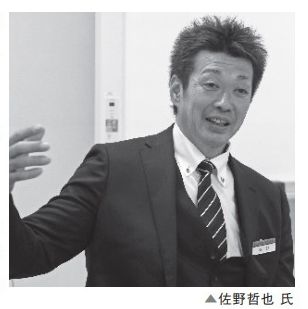
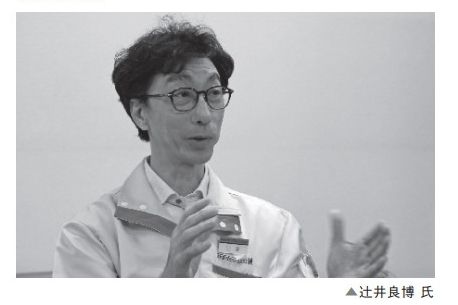
In 2005, following on from the mechanical business, they introduced the same system to the unit business. “Actually, when the mechanics introduced the system, my friends had mentioned TPiCS as a possible candidate, but it was a production management system recommended by the parent company, so we had no choice but to use another company’s product.” said Mr. Yoshihiro Tsujii, who was in charge of managing the unit business and was an advisor to the information system section of the management department.
By introducing the system in-house, the freedom has been more than before, but accounting processing and order processing between businesses still had to be done manually. The other implementation business remained the same as the parent company’s system, and the internal production management system continued to be a Three different structure. Unfortunately, a few years later, the system implemented by the mechanical business and the unit business ended up in a situation where the system maker withdrew from the business, and no matter what happened, they could not receive service.
Turn a pinch into a chance
The turning point came in 2015. The parent company was replaced by Kyoden. However, this created a big task for the person in charge of production management. The period of use of the system associated with the old parent company was limited to two years, during which time the new system had to be launched. However, the people in charge took the pinch as an opportunity and faced it positively. With Mr. Kobari and Mr. Sano as leaders, a project team was formed to build a new production management system, aiming for an ideal system. As a result, TPiCS was chosen.
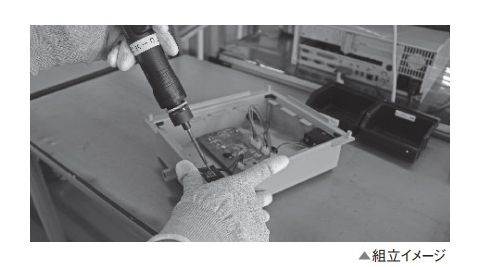
The decisive factor was, “In terms of functionality, we were able to respond to our requests and had a freedom,” said Mr. Kobari. “The method of information disclosure was easy to understand,” said Mr. Tsujii. “In addition to processing things in-house, the mechanical business also includes processes such as heat treatment and surface treatment, which we communicate with outsourced companies.” Mr. Sano said. As a way to proceed, they prioritized building a system with high urgency such as mass production as Step I, and took steps such as inventory, requesting expenses, prototyping of the mechanical division and individual order management etc. as Step II to start operation after a few months. However, the biggest problem was whether to completely unify the systems of the three businesses or separate them. “At first, we wanted to integrate everything because we were going to go to great lengths to create a new system.” However, as listened to Mr. Kosawell’s story, I thought that “there are many things that are more convenient to disperse.” (Mr. Tsujii)
Constructing a mechanism for decentralization and centralization
As a result, KPI decided to base each business on a distributed system with its own database. Each of the three businesses has its own characteristics. Integrating such different operations into one would make the system complicated. In addition, there are also sales and purchases between business divisions, so they decided that it would be better to make them independent in order to process them smoothly. However, KPI have standardized the input/output method and master registration, and have made it possible to do it automatically without relying on manual work even when compiling it company-wide.
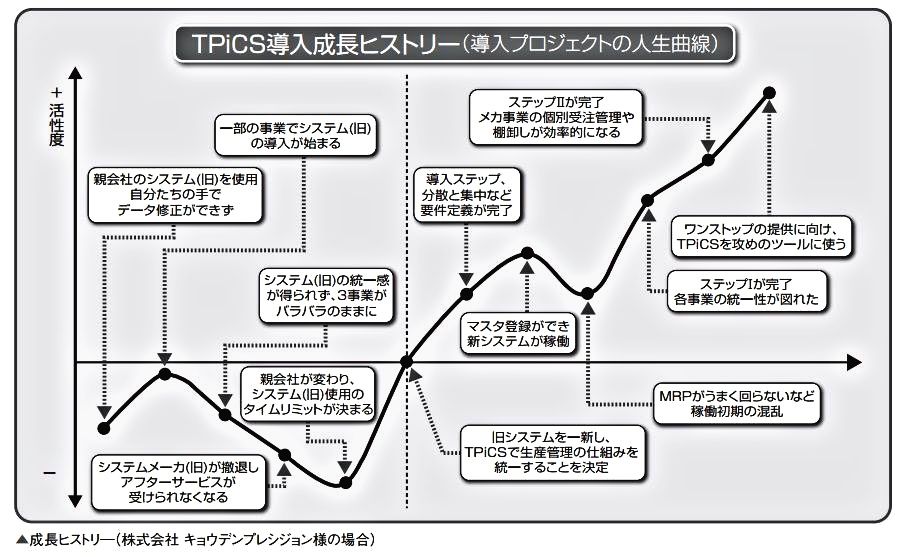
Completion of Step II, toward aggressive production management
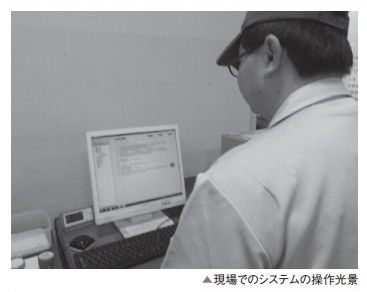
When running MRP as a company-wide production control, instead of running all three businesses at once, KPI start with the unit business, which handles set products, and then move on to the assembly and mechanical businesses in that order. In addition, the mechanical business receives orders for single items every day, so even if it is alone, MRP is turned every day. In other words, the mechanics business uses MRP for two purposes: calculation of the required amount for processing parts used in the unit and mounting business, and individual business. Currently, when they receive an order from Kyoden or an external order, they enter the data into TPiCS, create a production plan, and then issue parts arrangements and manufacturing instructions. Turn the MRP to confirm follow the instructions.
In this way, it is possible for the person in charge to decide everything from issuing to manufacturing and delivery. The system started operation in November 2016. Immediately after, there was some confusion over how to set up MRP, but once things were back in order, everything went smoothly. In March 2017, they completed Step II, including the inventory system.
Inventory is a simple system that uses barcodes, and has been well reputed by on-site employees. As they became accustomed to the new system, they began to make new improvement proposals, such as “If you do this, it will be easier to see.” Itagaki Yuya – Manager of the Information Systems Section, who was in charge of sorting out and summarizing requests from the workplace from the beginning, said: “We want to break away from the conventional defensive production management and use it as an offensive tool from now on.”
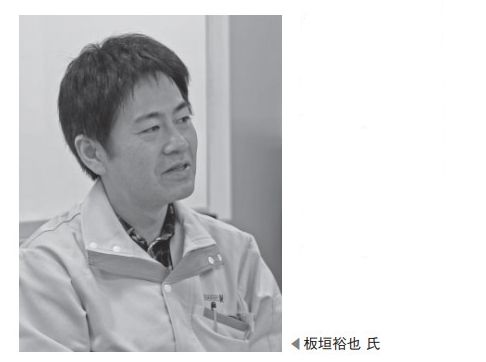