CÔNG TY KYODEN PRECISION (NHẬT BẢN)
TRIỂN KHAI hệ thống CÂN BẰNG GIỮA
QUẢN LÝ phân QUYỀN và tập trung
quản lý sản xuất Từ phòng thủ đến tấn công
1.Thực trạng:
Kyoden Precision đã hợp nhất quyền quản lý sản xuất của ba doanh nghiệp hoạt động riêng lẻ trong nhiều năm thành TPiCS. Trong khi duy trì sự độc lập của mỗi doanh nghiệp, chúng tôi đã xây dựng một hệ thống phân quyền và tập trung với sự đồng thuận của tất cả các bên.
- Kết quả:
- Do chuyển từ quản lý sản xuất phòng thủ sang tấn công nên hứng thú của người lao động trong công việc đã được cải thiện đáng kể.
- Việc cải tiến tại chỗ cũng đang đạt được nhiều tiến bộ.
- Mục tiêu:
Trong thời gian tới, chúng tôi sẽ tận dụng mọi chức năng của hệ thống quản lý sản xuất để nâng cao hiệu quả của từng lĩnh vực kinh doanh và hướng tới mục tiêu cho toàn công ty là cung cấp giải pháp một cửa hoàn toàn nội bộ.
Thách thức giải pháp một cửa
Kyoden Precision Co., Ltd. (Mifuku, thành phố Izunokuni, tỉnh Shizuoka, thường được gọi là KPI) được chia thành ba bộ phận kinh doanh: Gia công linh kiện như ép kim loại tấm, gia công, đúc các loại máy móc (Bộ phận cơ khí); lắp ráp bảng mạch in (Bộ phận lắp ráp), và Lắp ráp linh kiện (Linh kiện đơn lẻ).
Mặc dù mỗi bộ phận đều tiến hành kinh doanh riêng lẻ, nhưng “Mục tiêu của công ty là cung cấp giải pháp một cửa hoàn toàn nội bộ từ sản xuất linh kiện đến thành phẩm”, ông Satoru Akai – Giám đốc phân xưởng của nhà máy Sanfuku cho biết. Hơn nữa, tập đoàn Kyoden có bảy cơ sở sản xuất trong nước và một cơ sở sản xuất ở nước ngoài, bao gồm cả KPIs, ông Satoru Akai bày tỏ rằng: “Nếu tập hợp được sức mạnh của cả tập thể, chúng tôi có thể chế tạo ra bất kỳ máy móc hay thiết bị nào trên thế giới”.
Bắt đầu với quản lý sản xuất chỉ sử dụng
Hệ thống quản lý sản xuất của KPI đã có lịch sử hơn 30 năm. Tuy nhiên, trước năm 2000, công ty mẹ quản lý toàn bộ hệ thống, bên KPI chỉ sử dụng hệ thống để xử lý.
Vấn đề: Nếu mắc lỗi trong quá trình xử lý, KPI không thể tự sửa, chỉ có thể nhờ công ty mẹ sửa lỗi. ⇒ Hệ thống có mức độ tự do thấp
Do sự tích hợp nhiều lần của các công ty tiền thân của KPI, ba bộ phận KPI được đặt dưới sự quản lý của các công ty mẹ khác nhau và hệ thống quản lý sản xuất được sử dụng cũng khác nhau. Tuy nhiên, vì là một công ty nên nếu ba bộ phận không được kết hợp thành một thì không thể xử lý lỗi nếu vấn đề phát sinh. Do đó, quản lý của ba bộ phận đã tập trung họp vào một ngày cố định hàng tháng và ở lại đến khuya để thu thập dữ liệu bằng tay.
Tình trạng ba bên vẫn tiếp tục
Bắt đầu từ sự cố năm 2000, được cho là gây ra sự cố máy tính, bộ phận cơ khí đã kiến nghị với công ty mẹ để đưa ra một cơ chế quản lý sản xuất duy nhất. Sau lĩnh vực kinh doanh cơ khí, hệ thống tương tự cũng được triển khai trong doanh nghiệp đơn vị vào năm 2005. Với sự ra đời của hệ thống nội bộ, mức độ tự do đã tăng lên, nhưng việc xử lý kế toán và xử lý đơn hàng giữa các doanh nghiệp vẫn phải được thực hiện thủ công. Hệ thống trong lĩnh vực kinh doanh lắp ráp vẫn theo cơ chế của công ty mẹ, và việc quản lý sản xuất nội bộ vẫn được duy trì bằng hệ thống ba bên.
Thật không may, một vài năm sau, các hệ thống do các doanh nghiệp cơ khí và đơn vị giới thiệu đã bị nhà sản xuất hệ thống rút khỏi hoạt động kinh doanh và thậm chí nếu có sự cố xảy ra, họ không thể nhận được dịch vụ.
nắm bắt cơ hội
Bước ngoặt đến vào năm 2015. Công ty mẹ đã thay đổi, trở thành công ty con của Kyoden. Tuy nhiên, điều này làm tăng thêm rất nhiều công việc cho các nhân viên quản lý sản xuất. Hệ thống liên kết với công ty mẹ cũ bị giới hạn sử dụng trong hai năm nên hệ thống mới phải được đưa ra trong thời gian đó.
Tuy nhiên, những người phụ trách đã coi khó khăn đó như một cơ hội và tiếp cận một cách tích cực. Với sự lãnh đạo của ông Konee và ông Sano, chúng tôi quyết định thành lập một nhóm dự án để xây dựng một hệ thống quản lý sản xuất mới và hướng đến một hệ thống lý tưởng. Kết quả là, TPiCS đã được chọn.
Yếu tố quyết định là “có một mức độ tự do trong việc đáp ứng các yêu cầu của chúng tôi về mặt chức năng” (Ông Konee). “Cách tiết lộ thông tin dễ hiểu” (Ông Tsujii). “Ngoài việc tự gia công một số sản phẩm, bộ phận cơ khí của KPI còn hợp tác với các công ty thuê ngoài trong các quy trình như xử lý nhiệt và xử lý bề mặt, và TPiCS có chức năng cho phép phát hành và thanh toán suôn sẻ các đơn đặt hàng đó” (Ông Sano), v.v.
Về cách thức tiến hành, chúng tôi ưu tiên Xây dựng một cơ chế có tính cấp thiết cao như sản xuất hàng loạt (Bước I), và Áp dụng phương thức kiểm kê, yêu cầu chi phí, chạy thử nghiệm hệ thống và quản lý đơn hàng riêng lẻ trong bộ phận cơ khí (Bước II) trong vài tháng. Tuy nhiên, vấn đề lớn nhất là liệu có nên thống nhất hoàn toàn hay tách rời hệ thống của ba bộ phận.
“Ban đầu, chúng tôi muốn tích hợp mọi thứ vì như vậy sẽ tạo ra một hệ thống mới, nhưng khi nghe ông Kosawell nói rằng phân tách chúng sẽ tiện lợi hơn nhiều thì tôi đã hiểu ra.” (Ông Tsujii).
Xây dựng cơ chế phân tách và tập trung
Do đó, chúng tôi quyết định thiết lập các bộ phận trên một hệ thống phân tách, mỗi hệ thống có cơ sở dữ liệu riêng. Mỗi nghiệp vụ trong ba bộ phận này đều có những đặc điểm riêng. Việc tích hợp các nghiệp vụ khác nhau như vậy vào một sẽ làm hệ thống trở lên phức tạp hơn. Ngoài ra, cũng có các giao dịch mua bán giữa các bộ phận nên để xử lý chúng một cách suôn sẻ, chúng tôi quyết định rằng sẽ tốt hơn nếu để các bộ phận này độc lập. Hơn nữa, thống nhất chính xác phương thức đầu vào/đầu ra và đăng ký tổng thể khiến cho việc xử lý trong các bộ phận được thực hiện tự động mà không phải thủ công ngay cả khi tập hơp toàn thể công ty với nhau.
Hoàn thành bước II, chuyển sang quản lý sản xuất tấn công
Khi chạy MRP trong quản lý sản xuất toàn công ty, thay vì chạy cả ba bộ phận cùng một lúc, chúng tôi bắt đầu với bộ phận đơn vị xử lý các sản phẩm đã định sẵn, sau đó lần lượt chuyển sang bộ phận lắp ráp và bộ phận cơ khí. Ngoài ra, trong bộ phận cơ khí, các đơn đặt hàng linh kiện đơn được đặt mỗi ngày, vì vậy chúng tôi chạy MRP hàng ngày, ngay cả khi chỉ là các đơn hàng riêng lẻ. Nói cách khác, bộ phận cơ khí chạy MRP cho hai mục đích: tính toán số lượng cần thiết cho gia công linh kiện được sử dụng trong bộ phận đơn vị và bộ phận lắp ráp và kinh doanh cá thể. Hiện tại, khi chúng tôi nhận được đơn đặt hàng từ Kyoden hoặc đơn đặt hàng từ bên ngoài, chúng tôi đưa dữ liệu đó vào TPiCS để lập kế hoạch sản xuất và từ đó đưa ra kế hoạch chuẩn bị linh kiện và chỉ thị sản xuất. Xác nhận và chạy MRP theo chỉ thị đó.
Bằng cách này, người phụ trách có thể quyết định mọi thứ từ thanh toán đến sản xuất và vận chuyển. Hệ thống đã hoạt động vào tháng 11 năm 2016. Ngay sau đó, có một số nhầm lẫn về cách thiết lập MRP, nhưng sau khi được điều chỉnh chính xác, mọi thứ đã diễn ra suôn sẻ. Vào tháng 3 năm 2017, Bước II đã được hoàn thành, chẳng hạn như hệ thống kiểm kê. Kiểm kê là một hệ thống đơn giản sử dụng mã vạch và được các nhân viên trong khu vực sản xuất đánh giá rất tốt.
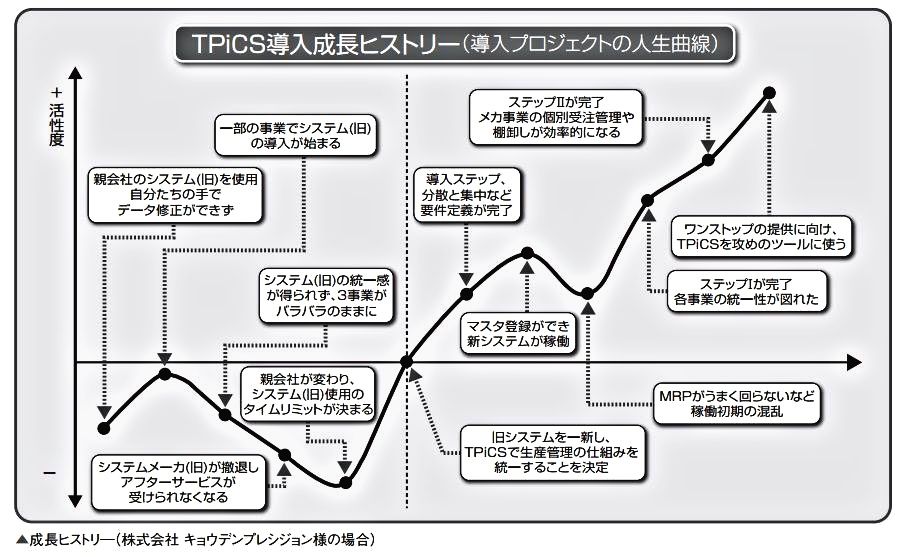